I. Introduction to Shearing Machine Hydraulic System
Shearing machines, a staple in metal processing industries, rely heavily on hydraulic systems to perform their tasks. The efficiency and effectiveness of shearing machines are significantly enhanced by the integration of hydraulic systems, which provide the necessary force and control to execute clean and accurate cuts.
Hydraulic systems use fluid pressure to generate force, allowing for the precise cutting of metal sheets in shearing machines. The primary aim of my article is to provide a comprehensive understanding of the hydraulic systems used in shearing machines.
II. Components of Shearing Machine Hydraulic System
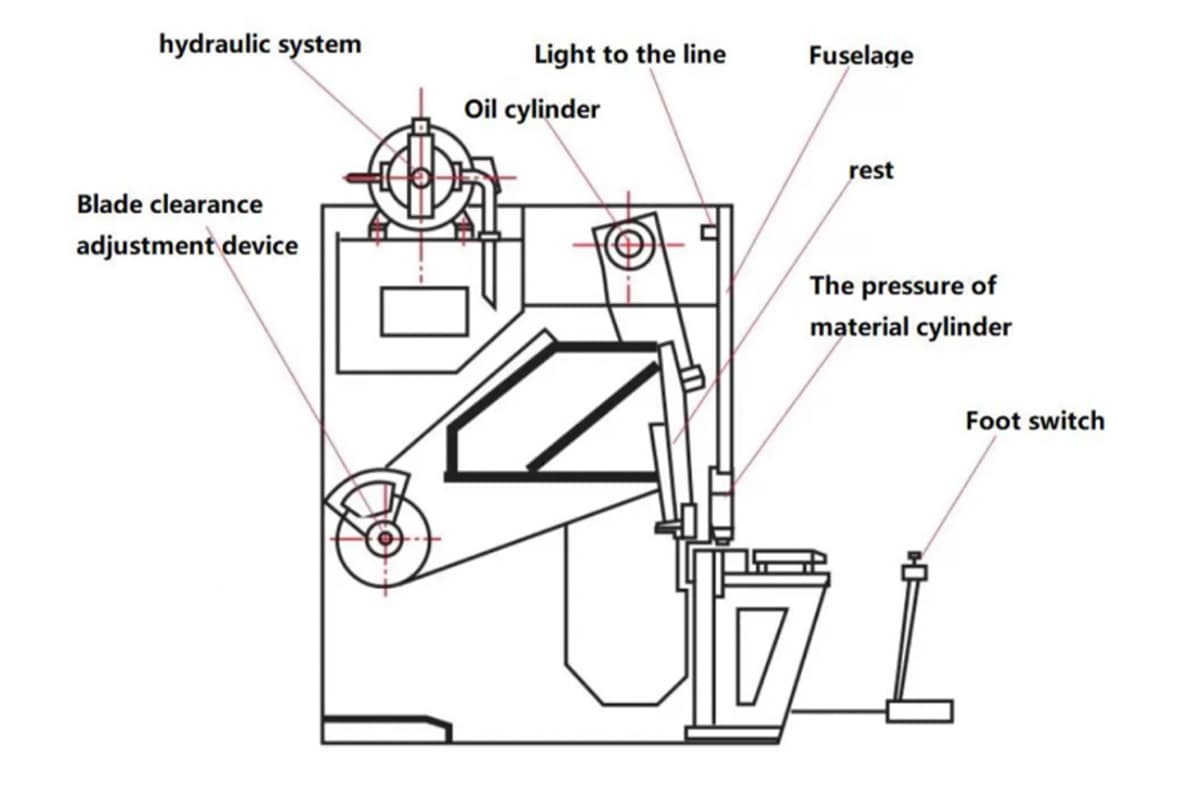
Each component of a hydraulic system in shearing machines plays a vital role in ensuring efficient, precise, and safe operation. By understanding these components and their functions, along with common issues and advancements, operators can optimize the performance and reliability of hydraulic shearing machines in various industrial applications.
Basic Principles of Hydraulics
Hydraulic systems operate on Pascal's Law, which states that pressure applied to a confined fluid is transmitted equally in all directions. This principle allows hydraulic systems to generate significant force using relatively small inputs. Key hydraulic principles include:
- Fluid Power: The ability to transmit force through a fluid medium.
- Pressure and Flow: The relationship between fluid pressure and flow rate, which determines the system’s power and speed.
Power Transmission Process
The power transmission process in hydraulic shearing machines involves several key steps:
- Energy Conversion:
- An electric motor converts electrical energy into mechanical energy to drive the hydraulic pump.
- Pressure Generation:
- The hydraulic pump pressurizes the hydraulic fluid, creating high-pressure fluid flow within the system.
- Controlled Distribution:
- Control valves direct and regulate the pressurized fluid to various components, such as hydraulic cylinders, which execute the shearing action.
- Mechanical Action:
- Hydraulic cylinders, driven by the pressurized fluid, convert hydraulic energy back into mechanical energy, moving the shearing blades to cut the metal sheets.
Role of Each Component in Operation
Hydraulic Pump
The hydraulic pump is the heart of the hydraulic system, responsible for converting mechanical energy into hydraulic energy. It drives the hydraulic fluid through the system, generating the necessary pressure to power the shearing process.
- Types of Hydraulic Pumps:
- Gear Pumps:Â Known for their simplicity and reliability, often used in moderate-pressure applications.
- Vane Pumps:Â Provide smoother operation and are suitable for moderate to high-pressure applications.
- Piston Pumps:Â Highly efficient and capable of handling high-pressure applications, often used in industrial settings.
- Common Issues:
- Cavitation:Â Occurs when air bubbles form in the hydraulic fluid, leading to reduced efficiency and potential damage. Regular maintenance and monitoring can prevent this issue.
Hydraulic Cylinders
Hydraulic cylinders convert hydraulic energy into mechanical energy. In shearing machines, these cylinders drive the upper blade or tool in a vertical motion, applying the force required to shear the material.
- Types of Hydraulic Cylinders:
- Single-Acting Cylinders:Â Apply force in one direction, suitable for simple applications.
- Double-Acting Cylinders:Â Apply force in both directions, enhancing operational efficiency and control.
- Common Issues:
- Seal Wear:Â Over time, seals can wear out, leading to leaks and reduced performance. Regular inspection and replacement of seals are essential.
Control Valves
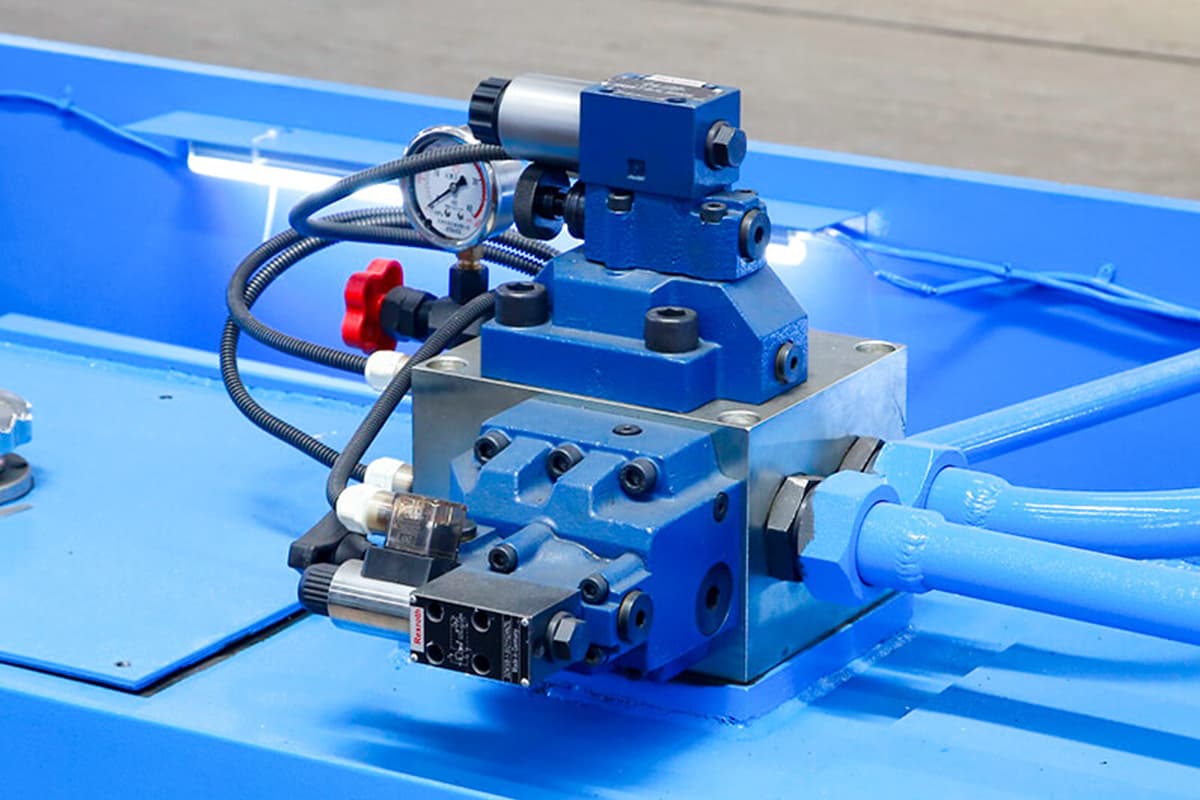
Control valves regulate the flow and direction of hydraulic fluid within the system, ensuring smooth and efficient operation.
- Types of Control Valves:
- Directional Control Valves:Â Direct the hydraulic fluid to various parts of the system.
- Pressure Control Valves:Â Maintain the desired pressure within the system.
- Flow Control Valves:Â Control the flow rate of the hydraulic fluid.
- Real-World Application:Â Precise control of hydraulic fluid flow is essential for achieving accurate cuts in shearing operations.
Hydraulic Fluid
Hydraulic fluid is the medium through which energy is transmitted in the hydraulic system. It must possess specific properties, such as low compressibility, high lubricity, and adequate thermal stability, to ensure efficient energy transfer and system longevity.
- Maintenance Tips:
- Regular Monitoring:Â Check for contamination and maintain proper fluid levels.
- Fluid Replacement:Â Follow the manufacturer's guidelines for fluid replacement intervals.
Reservoirs and Accumulators
Reservoirs store the hydraulic fluid and provide a means for heat dissipation, while accumulators store excess hydraulic energy and release it when needed to maintain system pressure.
- Functions:
- Stabilization:Â Help stabilize the hydraulic system, ensuring consistent performance.
- Heat Dissipation:Â Aid in removing air bubbles and cooling the hydraulic fluid.
Hydraulic Lines and Pressure Cylinder
Hydraulic lines transport the pressurized fluid from the pump to the hydraulic cylinders. The pressure cylinder aids in building up the force required for the shearing action.
- Design Considerations:
- Material:Â Use high-strength materials to withstand high pressures.
- Routing:Â Ensure proper routing to prevent pressure drops and fluid leaks.
Electrical Unit
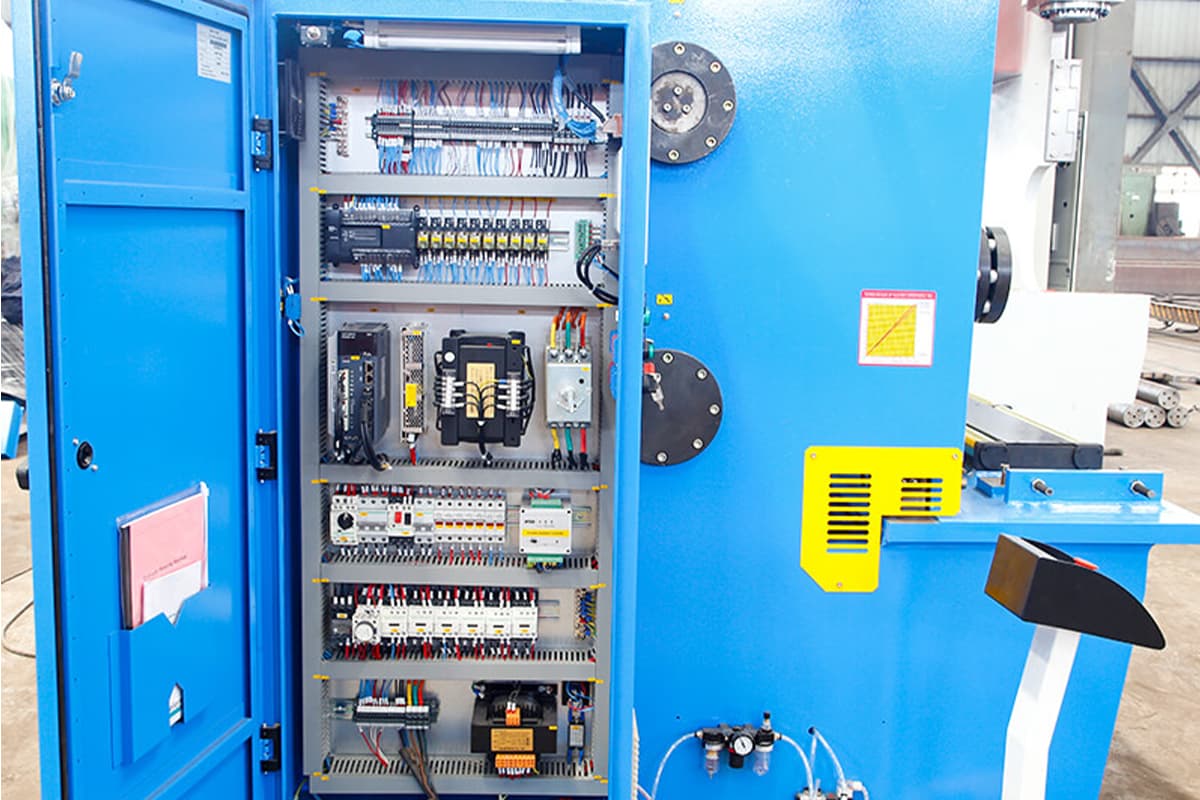
The electrical unit controls the hydraulic system, managing power, initiating the oil pump, and overseeing the overall operation.
- Components:
- Control Systems:Â Incorporate advanced control systems such as programmable logic controllers (PLCs) or computer numerical control (CNC) systems.
- Safety Features:Â Include emergency stop buttons and overload protection.
Upper and Lower Tool Holders
The upper and lower tool holders fix the shearing blades in place. The upper tool holder moves up and down along the slideway in the frame, driven by the hydraulic cylinder, to complete the shearing action.
- Alignment:Â Proper alignment is crucial for achieving accurate and consistent cuts.
- Material:Â Use high-strength materials to withstand the shearing force.
Pressing Device
The pressing device, often a hydraulic pressing plate, presses down the material during the shearing process. This prevents the material from moving, ensuring the quality and geometric accuracy of the cut.
- Function:Â Ensures the material remains stationary during the cut.
- Activation:Â Typically activated by hydraulic cylinders.
Safety and Control Mechanisms
Additional safety components include safety guards, baffles, and synchronization mechanisms.
- Safety Guards:Â Protect the operator from injury.
- Baffles:Â Provide protective measures for the machine.
- Synchronization Mechanisms:Â Ensure the upper and lower blades move in unison, achieving precise cuts.
CNC System (for CNC Hydraulic Shears)
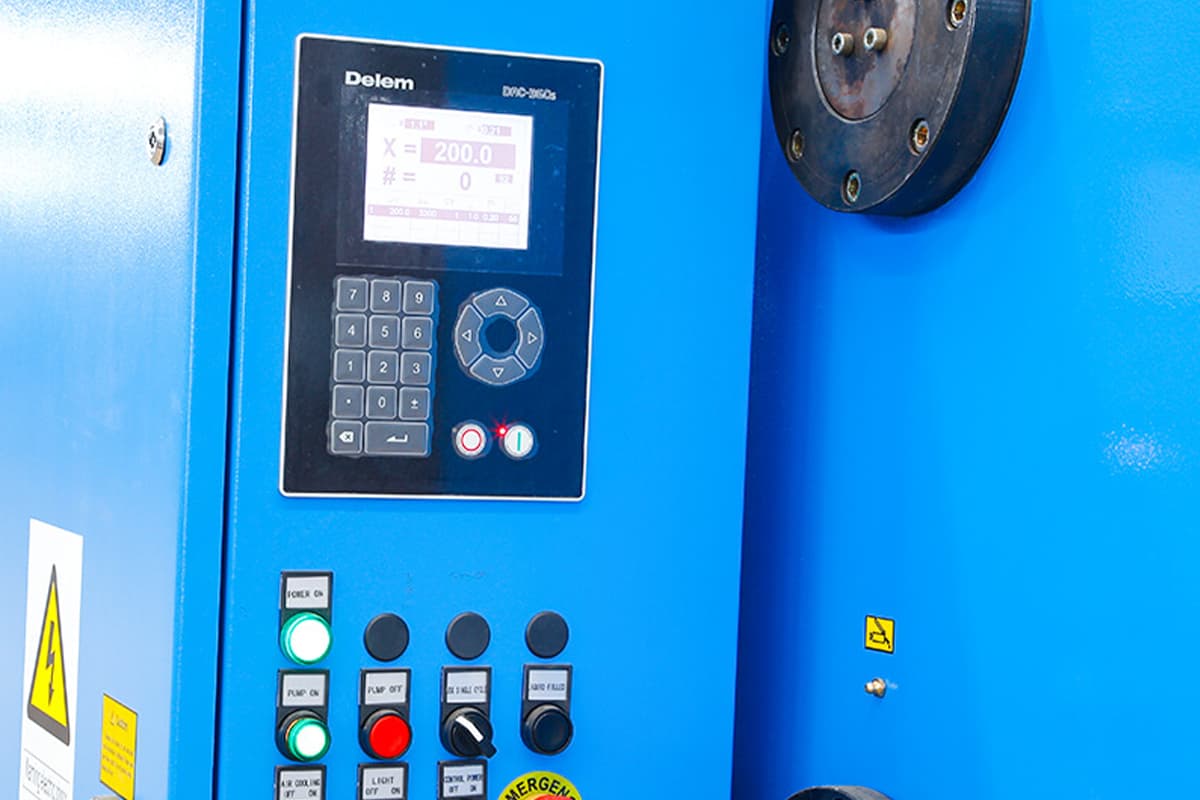
In CNC hydraulic shears, the CNC system integrates with the hydraulic system to provide precise control over the cutting process.
- Features:
- Automation:Â Enable automated and repetitive cutting tasks.
- Precision:Â Allow operators to input specific dimensions and angles for precise cuts.
III. Shearing Machine Hydraulic System Advantages
Precision and Control
One of the most significant advantages of hydraulic shearing machines is their superior precision and control. Hydraulic systems allow for fine adjustments of the shear angle and blade positioning, enabling accurate and consistent cuts with minimal material distortion.
- Example:Â In the aerospace industry, hydraulic shearing machines are used to cut titanium sheets with high precision, ensuring components meet stringent safety standards.
- Detailed Explanation:Â The ability to maintain a perpendicular motion to the lower blade ensures straighter cuts and reduces material waste. This perpendicular motion is important because it minimizes the bending of the material, leading to a higher quality cut and more efficient use of materials.
High Force Output
Hydraulic systems are known for their ability to generate significant force, which is crucial for cutting thicker and harder materials. The stable shear force provided by hydraulic systems ensures efficient cutting operations, even in demanding applications.
- Example:Â In the construction industry, hydraulic shears are used to cut through thick steel beams, demonstrating their capability to handle robust materials.
- Data Integration:Â Studies have shown that hydraulic shearing machines can extend the lifespan of blades by up to 50% compared to mechanical shears, thanks to their precise control and consistent force application.
Efficiency and Reliability
Hydraulic shearing machines offer smooth and reliable operation, reducing the risk of mechanical failures and downtime. The hydraulic transmission system provides a stable and continuous force, leading to more consistent performance compared to mechanical shears.
- Benefits:
- More energy-efficient, requiring less power to maintain consistent operation.
- Lower maintenance due to fewer moving parts, reducing operational costs and extending machine life.
Adjustable Shear Angle
The ability to adjust the shear angle is a notable feature of hydraulic shearing machines, particularly guillotine shears. This adjustability allows operators to optimize the shearing process based on the material thickness and desired cutting speed.
- Benefits:
- Achieve higher shearing capacity or speed, resulting in increased productivity.
- Save energy and reduce working time, further enhancing operational efficiency.
Longer Blade and Cylinder Life
Hydraulic shearing machines are designed to extend the life of critical components, such as blades and oil cylinders. The straight-line motion of guillotine shears, combined with the absence of additional lubrication needs for the oil cylinders, contributes to their longevity.
- Example:Â The blades on guillotine shears can be utilized for four-sided cutting, effectively doubling their service life compared to pendulum-type shears.
- Data Integration:Â Hydraulic shears can extend blade life by up to 50% due to consistent force application and precise control, reducing the frequency of replacements and associated maintenance costs.
Wider Application Range
Hydraulic shearing machines are versatile and can handle a wide range of materials and thicknesses. This adaptability makes them suitable for various industrial applications, from cutting thin metal sheets to processing thicker plates.
- Example:Â In the automotive industry, hydraulic shears are used to cut different types of metals, including steel and aluminum, for various components.
- Benefits:Â The ability to work with different materials expands their applicability across multiple sectors, including metal fabrication, automotive, aerospace, and construction.
Enhanced Safety Features
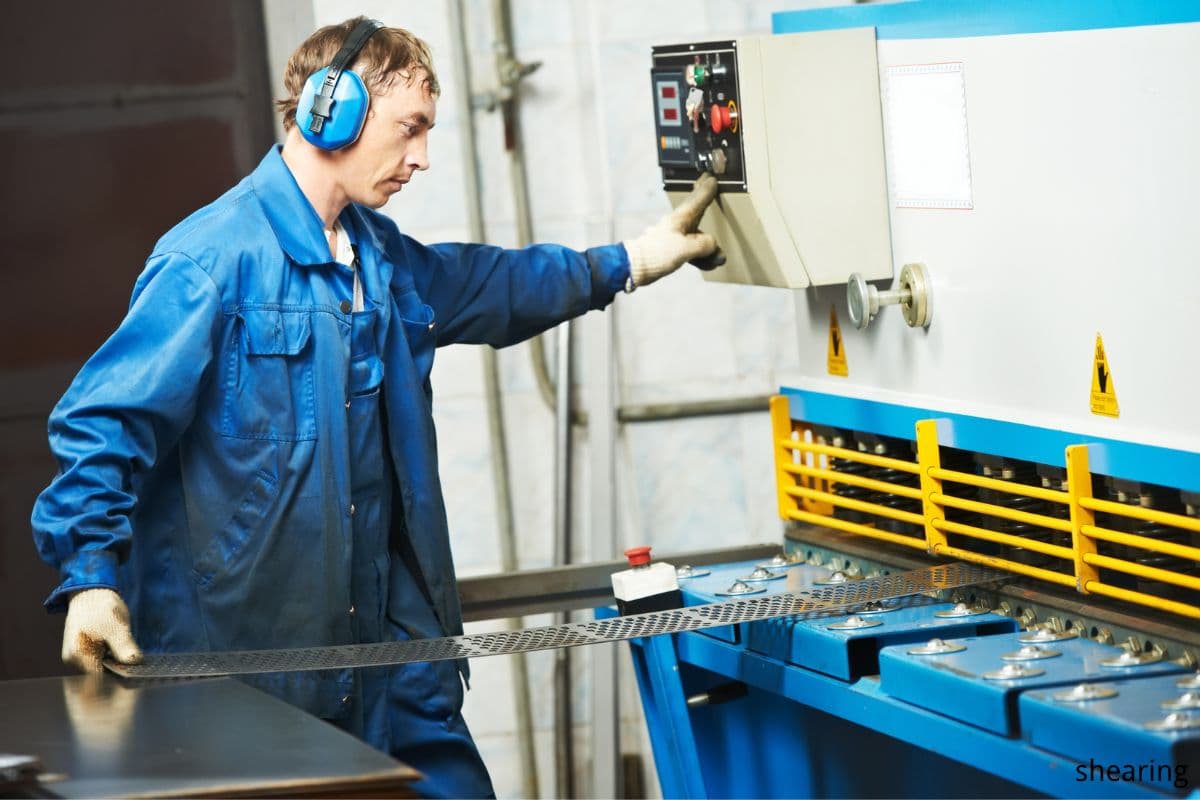
Hydraulic shearing machines often come equipped with advanced safety features to protect operators and prevent accidents. These features may include safety guards, emergency stop buttons, and overload protection mechanisms.
- Benefits:
- Smooth operation reduces the risk of sudden mechanical failures, enhancing overall safety.
- Modern hydraulic shears may incorporate numerical control systems and back gauge mechanisms, further improving precision and operator safety.
Energy Efficiency and Low Maintenance
Hydraulic shearing machines are generally more energy-efficient than their mechanical counterparts. They do not require as much energy to maintain consistent operation and often do not need additional cooling systems, which can be energy-intensive.
- Benefits:
- Lower maintenance requirements due to simpler design and fewer moving parts.
- Reduced operational costs and longer machine life.
IV. Troubleshooting and Maintenance of Hydraulic Systems
Common Issues and Their Solutions
Low System Pressure
Symptoms:
- Slow or incomplete cutting actions.
- Reduced force output.
Possible Causes and Solutions:
- Relief Valve Set Too Low: Adjust the relief valve to the correct pressure setting using a pressure gauge.
- Worn Pump Parts: Internal leakage due to worn rotor sets and other components can reduce pressure. Replace worn parts to restore system efficiency.
Pump Not Delivering Fluid Properly
Symptoms:
- Erratic or no fluid flow.
- Reduced system performance.
Possible Causes and Solutions:
- Incorrect Rotation Direction: Ensure the pump is rotating in the direction indicated by the arrow on the pump body. Stop the pump immediately if the rotation is incorrect to prevent damage.
- Broken Drive Shaft or Sheared Shaft Key: Inspect the drive shaft for breaks or the shaft key for shearing. Repair or replace as necessary.
- Blocked Intake Pipe or Heavy Oil Viscosity: Drain and replace the hydraulic fluid with the correct viscosity. Clean or replace the intake pipe if blocked.
- Air Leaks at Intake Connections: Tighten intake connections to eliminate air leaks. Bleed the hydraulic system to remove trapped air.
Leaks
Symptoms:
- Visible fluid leaks.
- Reduced fluid levels.
Possible Causes and Solutions:
- Seal Leaks: Check and replace worn or damaged seals. Ensure that system pressure does not exceed seal specifications.
- External Leaks: Inspect hoses, fittings, and connections for visible leaks. Replace damaged hoses and tighten connections.
- Internal Leaks: Inspect pumps, valves, and actuators for signs of internal leakage. Maintain proper fluid levels and use high-quality filters to prevent contamination.
Excessive Noise
Symptoms:
- Unusual sounds during operation.
- Vibrations in the hydraulic system.
Possible Causes and Solutions:
- Clogged Intake Strainer/Pipe: Clean or replace the intake strainer and ensure unrestricted fluid flow to the pump to avoid cavitation.
- Defective Bearings: Replace worn or damaged bearings and inspect the pump shaft for wear.
- Air Leaks at Pump Intake Pipe Joints or Shaft Seal: Tighten joints and replace seals to eliminate air ingress.
- Incorrect Drive Speed or Misaligned Coupling: Ensure the motor runs at the correct speed and align the coupling shafts properly.
Overheating
Symptoms:
- High fluid temperatures.
- Reduced system performance.
Possible Causes and Solutions:
- Excessive Workload or High Duty Cycle: Reduce workload or allow the system to cool periodically. Ensure the hydraulic reservoir is adequately filled and properly ventilated.
- Failed or Worn Components: Inspect and replace components with internal leakage. Ensure proper functioning of the heat exchanger and maintain airflow around the reservoir.
Hydraulic Fluid Contamination
Symptoms:
- Degraded system performance.
- Increased wear on components.
Possible Causes and Solutions:
- Particulates: Install high-quality filters and replace them regularly to remove dirt and debris.
- Water Contamination: Use water-absorbing filters and ensure proper sealing of the hydraulic reservoir.
- Air Entrapment: Bleed the hydraulic system to remove trapped air and inspect for leaks that could introduce air.
Preventive Maintenance Tips
Oil Maintenance
- Monitor Fluid Levels: Regularly check and maintain hydraulic fluid levels. Low fluid levels can damage pumps and reduce system efficiency.
- Fluid Quality: Use the correct type and grade of hydraulic fluid as specified by the manufacturer. Replace fluid at recommended intervals to prevent contamination and degradation.
Filter Maintenance
- Regular Inspection: Inspect and replace hydraulic filters as indicated by filter condition indicators. Clean or replace breather caps, fill screens, and breather filters to prevent contamination.
- Filter Replacement: Follow a routine schedule for replacing filters to ensure optimal fluid cleanliness and system performance.
Hose and Pipe Inspection
- Visual Checks: Regularly inspect all hydraulic hoses and pipes for signs of damage, such as pinching, kinking, fraying, or corrosion. Ensure fittings are snug but not overly tight to prevent leaks.
- Preventive Measures: Replace damaged hoses and pipes before they fail to avoid sudden system breakdowns.
System Temperature Monitoring
- Temperature Checks: Regularly monitor the system temperature using thermometers or built-in sensors. High temperatures can indicate issues with the cooling system or excessive workload.
- Cooling System Maintenance: Ensure the heat exchanger and cooling circuit components are clean and functioning correctly. Maintain proper airflow around the hydraulic reservoir.
Routine Checks
- Condition Monitoring: Use condition monitoring systems to identify potential issues such as clogged filters or abnormal pressure readings.
- Component Inspections: Regularly inspect accumulators, pressure-control valves, pressure-reducing valves, pump compensators, and relief valves to ensure they are operating correctly and maintaining proper system pressures.
V. Frequently Asked Questions
1. What is a hydraulic system in a shearing machine?
A hydraulic system in a shearing machine uses fluid mechanics to generate and control high forces required for cutting metal sheets. It consists of components like hydraulic pumps, cylinders, control valves, and hydraulic fluid, which work together to convert mechanical energy into hydraulic energy and back into mechanical energy for precise and efficient cutting.
2. Can hydraulic shearing machines be used for materials other than metal?
Yes, hydraulic shearing machines can be used for materials other than metal, such as plastics and composites, depending on the machine's design and specifications. However, the cutting parameters may need to be adjusted to accommodate the different properties of these materials. It's essential to consult the manufacturer's guidelines to ensure the machine is suitable for cutting non-metallic materials.
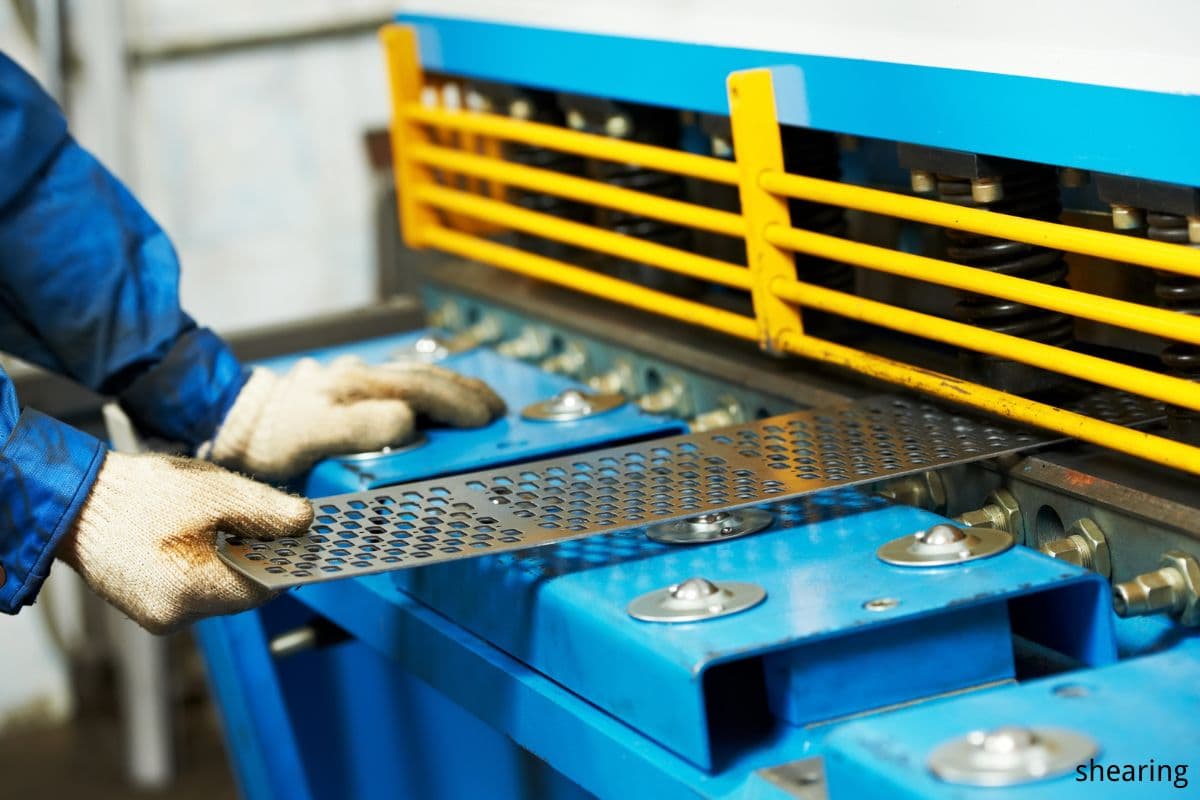
3. What safety measures should be taken when operating a hydraulic shearing machine?
- Personal Protective Equipment (PPE): Operators should wear appropriate PPE, including gloves, safety goggles, and protective clothing.
- Machine Guarding: Ensure all safety guards and barriers are in place and functioning correctly to prevent accidental contact with moving parts.
- Training: Only trained and certified personnel should operate hydraulic shearing machines. Comprehensive training includes understanding machine controls, safety protocols, and emergency procedures.
- Lockout/Tagout Procedures: Implement lockout/tagout procedures during maintenance to prevent accidental machine start-up.
- Emergency Stops: Familiarize operators with the location and operation of emergency stop buttons.
- Regular Inspections: Conduct routine inspections to identify and rectify potential safety hazards, such as hydraulic leaks or worn components.
saw blade,Cutting Circular Saw Blade,Tungsten carbide circular saw blade,Circular Saw Blade,paper saw blade,saw knives
Zigong Brace Cemented Carbide Co.,Ltd , https://www.bracecarbide.com