I. Introduction
Laser cutting machine tools represent a significant advancement in the field of industrial manufacturing, offering precision, versatility, and efficiency. These machines utilize a focused laser beam to cut through materials, providing clean and accurate edges with minimal waste.
Understanding the mechanics and applications of laser cutting tools is essential for leveraging their full potential. In this article, we will delve into the intricacies of laser cutting machines.
This involves comprehending the different types of lasers, their unique features, and the specific advantages they bring to industrial operations.
II. Types of Laser Cutting Machines
Introduction to Laser Cutting Technology
Laser cutting technology revolutionized the manufacturing industry by enabling precise, efficient, and high-speed cutting of various materials. This technology uses a focused laser beam to melt, burn, or vaporize material, creating intricate cuts with minimal waste. Laser cutting is integral to industries ranging from automotive and aerospace to electronics and textiles due to its versatility and precision.
CO2 Laser Cutting Machines
CO2 laser cutting machines are among the most widely used types of laser cutters. They operate using a gas mixture that primarily consists of carbon dioxide (CO2), nitrogen, and helium. These machines are highly efficient for cutting, engraving, and marking a wide range of materials, including non-metals and metals.
Key Features
- Wavelength:Â CO2 lasers typically have a wavelength of 10.6 micrometers, which is highly effective for cutting non-metallic materials due to their high absorption rate.
- Material Compatibility:Â Ideal for cutting organic materials such as wood, acrylic, glass, and textiles. They can also cut metals, but require higher power levels and special configurations.
- Cut Quality:Â Known for producing smooth and clean cuts with minimal burring.
Applications
- Signage and Advertising:Â Used for cutting and engraving acrylic and other materials to create signs and displays.
- Textile Industry:Â Ideal for cutting fabrics and leather with intricate patterns.
- Packaging Industry:Â Employed in cutting cardboard and other packaging materials.
Advantages and Limitations
- Advantages:Â CO2 lasers offer high-speed cutting capabilities with smooth edges, making them ideal for precise and intricate designs. They are relatively low-cost and have a long operational lifespan.
- Limitations:Â Their primary limitation is their reduced efficiency in cutting reflective metals like aluminum and copper. Additionally, maintenance can be demanding due to the need for regular CO2 gas refills and optical alignment.
Fiber Laser Cutting Machines
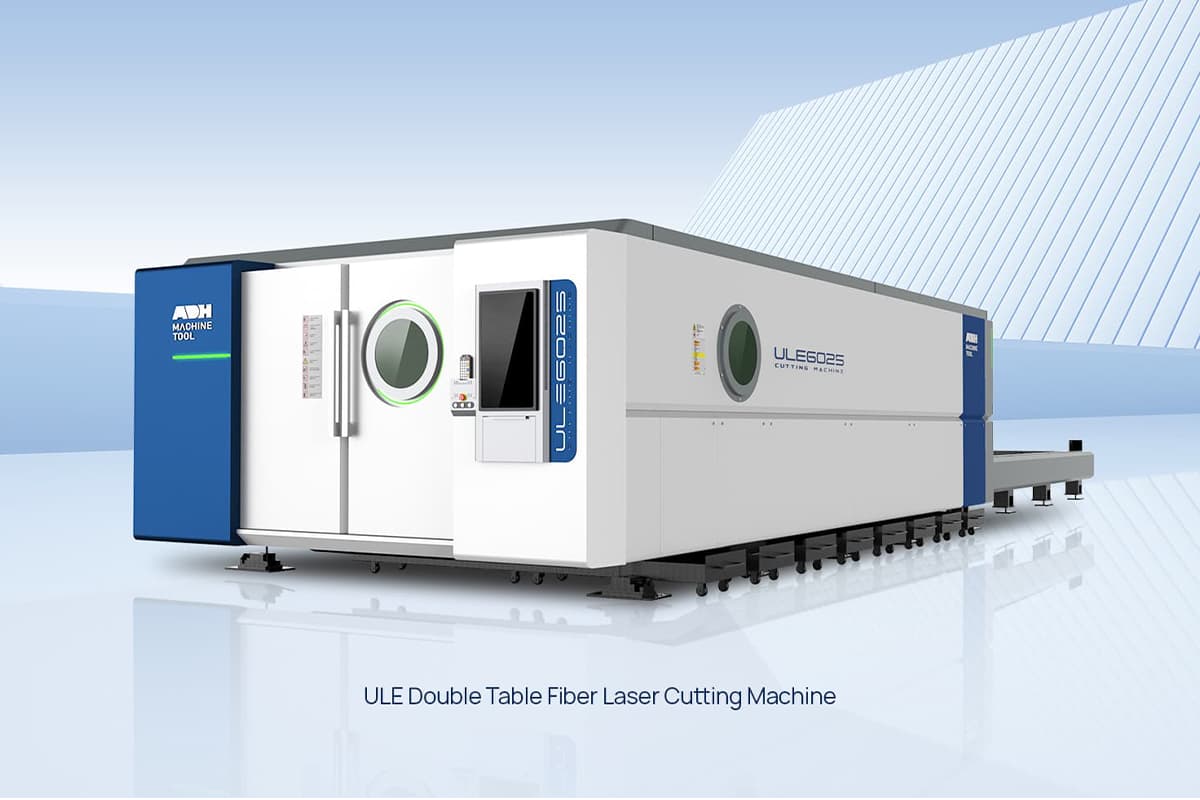
Fiber laser cutting machines utilize a solid-state laser, where the laser beam is generated by a series of diodes and transmitted through a flexible optical fiber. Fiber lasers use optical fibers doped with rare-earth elements to amplify the laser beam.
These machines are known for their high efficiency, precision, and versatility, making them suitable for cutting a wide range of materials, particularly metals.
Key Features
- Wavelength:Â Fiber lasers have a wavelength of approximately 1.06 micrometers, which allows for high absorption by metals, leading to efficient cutting.
- Energy Efficiency:Â Fiber lasers are more energy-efficient than CO2 lasers, offering higher cutting speeds and lower operating costs.
- Maintenance:Â Require less maintenance compared to CO2 lasers, as they have fewer moving parts and no need for gas mixtures.
Applications
- Automotive Industry:Â Used for cutting and welding automotive components with high precision.
- Aerospace Industry:Â Suitable for cutting lightweight metals and alloys used in aircraft manufacturing.
- Electronics Manufacturing:Â Employed in cutting thin metal sheets and components for electronic devices.
Advantages and Limitations
- Advantages:Â Fiber lasers boast faster cutting speeds, lower maintenance requirements, and higher electrical efficiency. They can effectively cut reflective metals and offer superior beam quality.
- Limitations:Â The initial investment for fiber lasers can be higher compared to CO2 lasers. They are also less effective in processing non-metal materials, making them less versatile for mixed-material applications.
Nd:YAG Laser Cutting Machines
Nd:YAG (Neodymium-doped Yttrium Aluminum Garnet) laser cutting machines use a solid-state laser, where the laser medium is a crystal of YAG doped with neodymium ions. These machines are known for their high peak power and ability to cut and weld a variety of materials with precision.
Key Features
- Wavelength:Â Nd:YAG lasers typically operate at a wavelength of 1.064 micrometers, similar to fiber lasers, making them effective for metal processing.
- Pulse Mode:Â Capable of operating in both continuous wave and pulsed modes, allowing for versatility in cutting and welding applications.
- Precision:Â Provide high precision and control, making them suitable for delicate and detailed work.
Applications
- Medical Device Fabrication:Â Used for cutting and welding medical devices and instruments with high precision.
- Jewelry Manufacturing:Â Employed in cutting and engraving precious metals and gemstones.
- Mold and Die Making:Â Suitable for cutting and engraving intricate patterns on molds and dies.
Advantages and Limitations
- Advantages:Â Crystal lasers provide excellent beam quality and precision, making them perfect for detailed tasks that require accuracy. They can cut through both metals and certain non-metals with fine control.
- Limitations:Â These machines typically suffer from shorter lifespans due to the degradation of the laser crystal. The cost of crystal replacement and overall maintenance can be higher compared to other laser types.
Comparative Analysis Table
Laser Type | Wavelength | Power Efficiency | Notable Features | Suitable Materials | Maintenance | Key Industries |
CO2 Laser | 10.6 micrometers | Moderate | Smooth cuts, versatile | Non-metals, some metals | Moderate (Gas refills) | Signage, Textiles, Packaging |
Fiber Laser | 1.06 micrometers | High | Energy-efficient, high precision | Metals (reflective/non-reflective) | Low | Automotive, Aerospace, Electronics |
Nd:YAG Laser | 1.064 micrometers | High | High peak power, versatile | Metals and fine non-metals | High (Crystal care) | Medical, Jewelry, Mold Making |
III. Key Components of Laser Cutting Machines
Laser Source
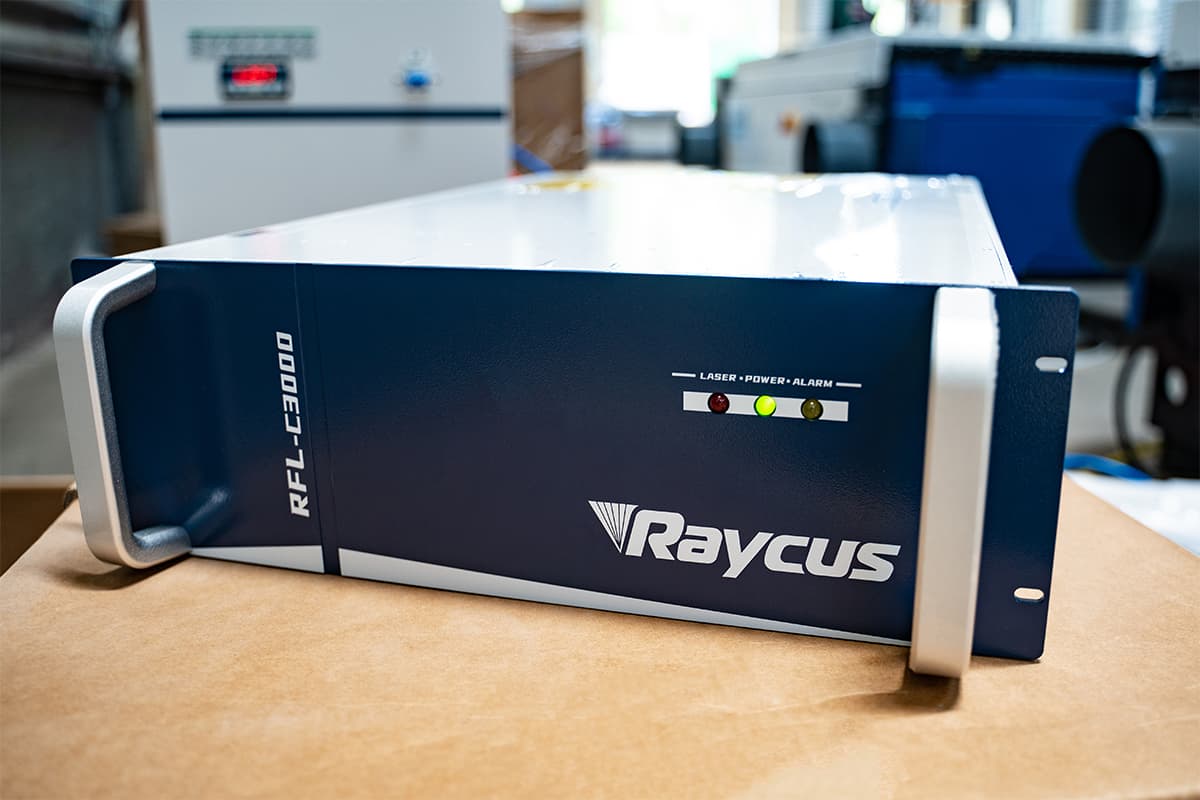
The laser source, often referred to as the heart of the laser cutting machine, generates the powerful beam necessary for cutting materials. Depending on the type of laser cutting machine, the laser source can vary:
- CO2 Laser Source: Uses a gas mixture primarily composed of carbon dioxide, nitrogen, and helium to produce a laser beam. Ideal for cutting non-metals and some metals. For instance, CO2 lasers are preferred for cutting wood, acrylic, and certain plastics due to their efficiency in handling these materials.
- Fiber Laser Source: Utilizes a series of diodes to generate a laser beam, which is then transmitted through a flexible optical fiber. Known for its high efficiency and suitability for cutting metals. Fiber lasers are often used in industries requiring high-speed cutting of metals, such as stainless steel and aluminum.
- Nd:YAG Laser Source: Employs a solid-state crystal doped with neodymium to produce a laser beam. Effective for both cutting and welding applications, particularly in metals. Nd:YAG lasers are commonly used in scenarios where both cutting and welding precision are required, such as in the automotive industry.
Cutting Head
The cutting head directs the laser beam precisely onto the material surface, ensuring accurate cuts. It typically consists of several sub-components:
- Focusing Lens: Concentrates the laser beam to a fine point, increasing its intensity for precise cutting. The lens must be kept clean and properly aligned to ensure optimal performance.
- Nozzle: Directs the assist gas (such as oxygen, nitrogen, or air) onto the cutting area. The assist gas helps to remove molten material and enhances cutting quality by preventing oxidation.
- Height Sensor: Maintains a consistent distance between the cutting head and the material surface, adjusting the height in real-time to accommodate variations in material thickness and surface irregularities.
Control System
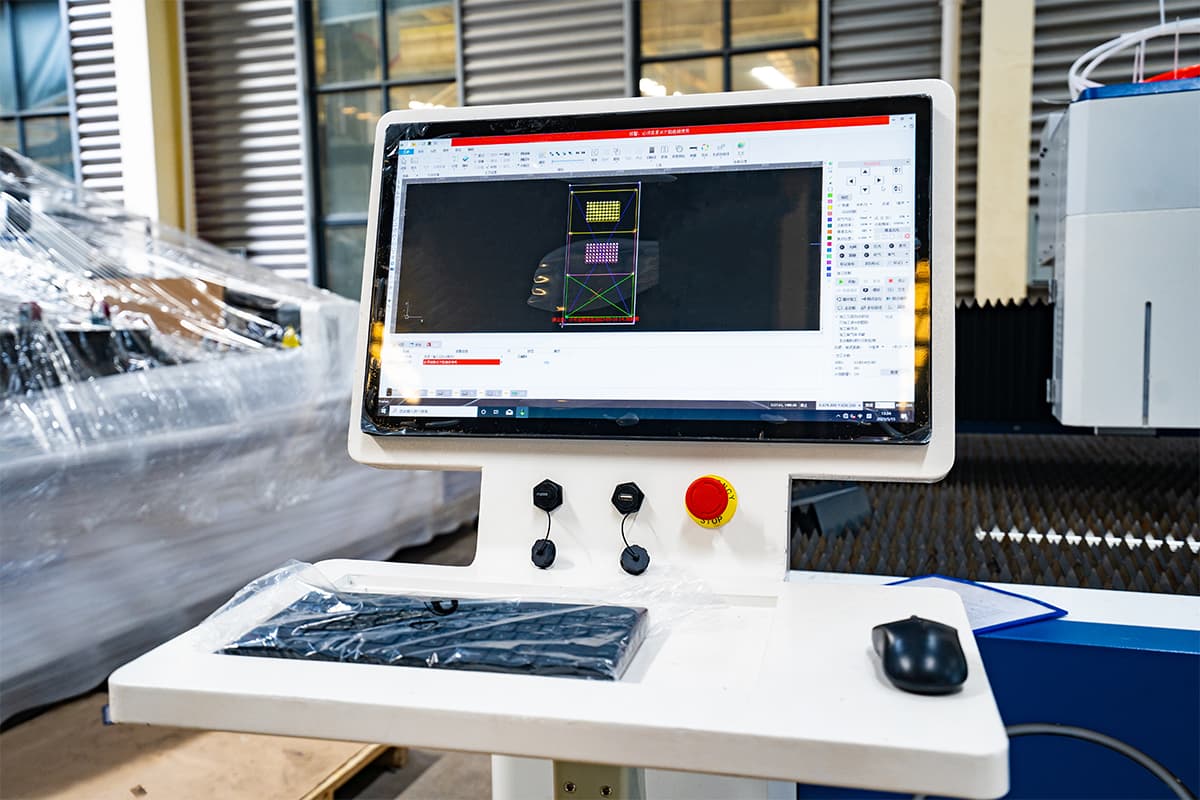
Acting as the brain of the machine, the control system manages all operational parameters, ensuring each cutting task is executed with precision. It includes:
- CNC Controller: A computer numerical control (CNC) system that interprets the cutting design and generates the necessary commands to control the movement of the cutting head and other machine components. The CNC controller ensures that the cutting path is followed accurately, which is crucial for intricate designs.
- Software Interface: Allows operators to input cutting parameters, design files, and monitor the cutting process. Advanced software may include features for optimizing cutting paths, nesting parts to minimize material waste, and real-time diagnostics.
- Sensors and Feedback Mechanisms: Continuously monitor machine performance and cutting quality, providing feedback to the control system to make real-time adjustments.
Worktable
The worktable securely holds the material in place during the cutting process, ensuring stability and precision. Key features of the worktable include:
- Material Support: The worktable is designed to support various materials, ensuring they remain flat and stable during the cutting process. It may include a grid or honeycomb structure to minimize contact with the laser beam and reduce back reflections.
- Movement Mechanism: In some machines, the worktable itself may move to position the material under the cutting head. This can be achieved through linear guides, ball screws, or other precision movement systems.
- Clamping System: Ensures the material is securely held in place, preventing shifts during cutting that could compromise accuracy.
Assist Gas System
The assist gas system delivers specific gases to the cutting head, aiding in the cutting process by enhancing quality and cutting speed. Different gases serve different purposes:
- Oxygen: Enhances the cutting of metals by promoting oxidation, which helps to blow away molten material. Oxygen is often used for cutting carbon steel, as it speeds up the cutting process.
- Nitrogen: Used for cutting non-metals and stainless steel, preventing oxidation and producing cleaner cuts. Nitrogen is preferred for materials where oxidation would negatively impact the edge quality, such as stainless steel.
- Air: A cost-effective option for cutting certain materials, though it may not provide the same quality as specialized gases. Air can be used for cutting materials like aluminum and mild steel in less critical applications.
Cooling System
The cooling system prevents the laser source and other components from overheating, ensuring consistent performance and extending the machine’s lifespan. It typically includes:
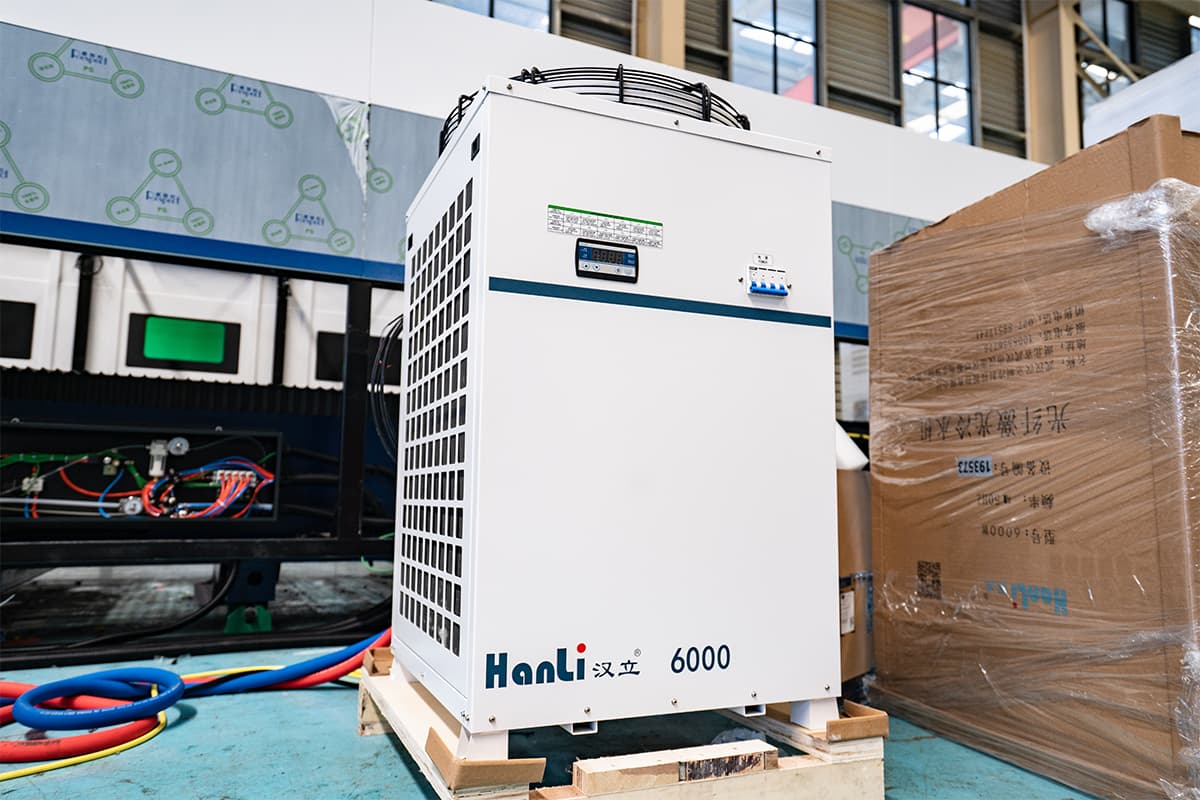
- Water Chiller: Circulates cooled water through the laser source and other heat-sensitive components, dissipating heat effectively.
- Heat Exchangers: Transfer heat away from critical components, maintaining a stable operating temperature.
Dust and Fume Extraction System
Laser cutting generates dust and fumes that need to be safely removed to ensure a clean working environment and protect the machine's components. The extraction system includes:
- Fume Extractors: Capture and filter out harmful particulates and gases generated during cutting.
- Dust Collectors: Collect larger particles and debris, preventing them from settling on machine components or the worktable.
IV. Applications of Laser Cutting Machine Tools
Laser cutting machine tools have become indispensable in various industries due to their precision, efficiency, and versatility. These advanced tools are capable of cutting a wide range of materials with intricate designs and minimal waste.
Below, we explore the prominent applications of laser cutting machine tools across different sectors, enhanced with specific examples, technical details, and future trends.
Automotive Industry
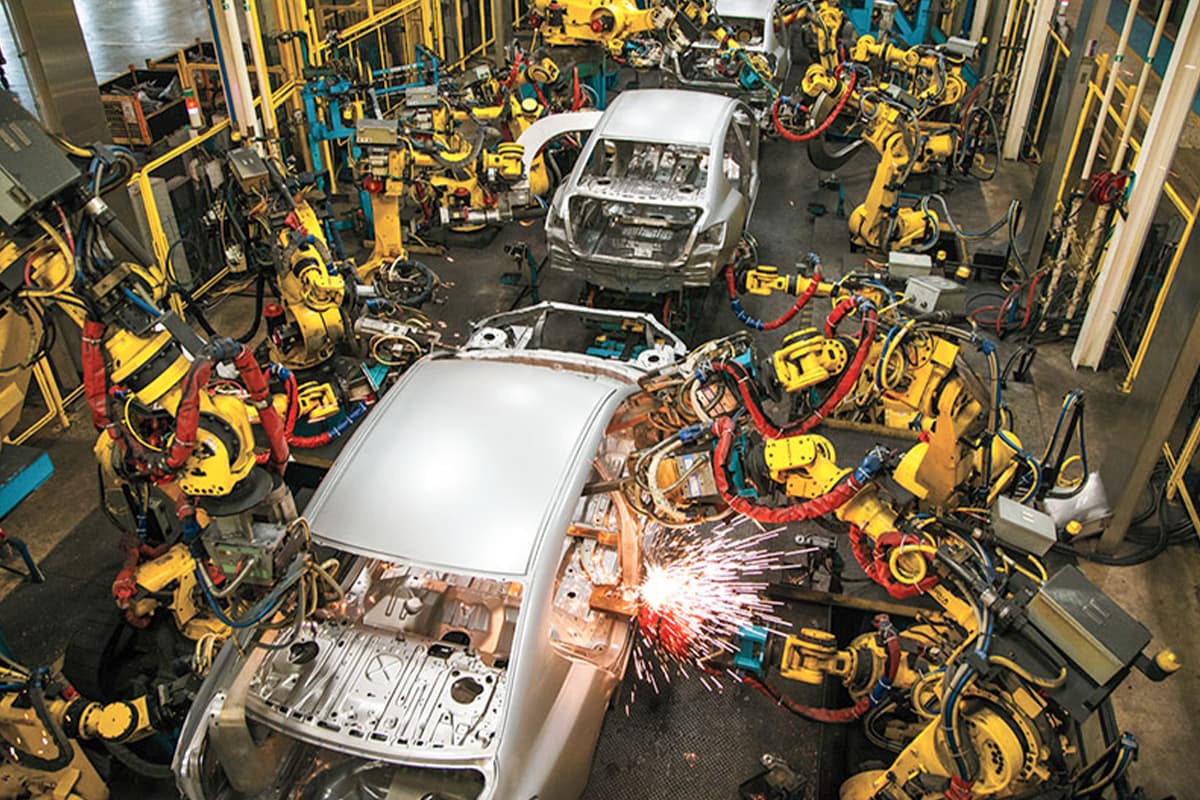
The automotive industry heavily relies on laser cutting technology for the manufacturing of various components. The precision and speed of laser cutting machines make them ideal for producing complex parts that meet stringent quality standards.
- Component Manufacturing: Laser cutting is used to fabricate parts such as airbag components, brake pads, and dashboards. For instance, Ford uses laser cutting to produce precise airbag components, ensuring each part meets safety standards.
- Prototyping and Customization: Laser cutting allows for rapid prototyping, enabling automotive designers to quickly iterate and test new designs. Additionally, it facilitates the customization of parts for limited edition models or specific customer requirements.
- Weight Reduction: Lightweight materials like aluminum and composites are commonly used in modern vehicles to improve fuel efficiency. Laser cutting machines handle these materials with ease, maintaining the structural integrity of the parts while reducing weight.
Aerospace Industry
The aerospace industry demands extremely high precision and reliability, making laser cutting an essential technology in this sector. Laser cutting machines are used to process various materials, including metals and composites, critical for aircraft manufacturing.
- Aircraft Components: Laser cutting is employed to produce intricate parts such as engine components, brackets, and airframe structures. For example, Boeing uses laser cutting for titanium parts in their aircraft, ensuring parts meet strict tolerances and performance standards.
- Material Efficiency: Given the high cost of aerospace materials like titanium and carbon fiber composites, minimizing waste is crucial. Laser cutting machines enable efficient material usage by optimizing cutting paths and reducing scrap.
- Maintenance and Repair: Laser cutting is not only used in manufacturing but also in the maintenance and repair of aircraft. It allows for precise removal of damaged sections and the fabrication of replacement parts with exact specifications.
Electronics Manufacturing
In the electronics industry, where miniaturization and precision are paramount, laser cutting machines play a vital role in producing small and intricate components.
- Printed Circuit Boards (PCBs): Laser cutting is used to cut and engrave PCBs, ensuring precise pathways and connections for electronic components. The accuracy of laser cutting helps in achieving the high-density interconnections required in modern electronics.
- Micromachining: Laser cutting machines are capable of micromachining, which involves cutting and drilling extremely small features. This is essential for the production of components like microchips, sensors, and connectors.
- Custom Enclosures: Laser cutting is also used to create custom enclosures for electronic devices, providing precise cutouts for buttons, displays, and connectors.
Medical Device Fabrication
The medical industry requires high precision and cleanliness in the manufacturing of devices and instruments. Laser cutting technology meets these stringent requirements, making it a preferred choice for medical device fabrication.
- Surgical Instruments: Laser cutting is used to manufacture surgical instruments such as scalpels, forceps, and scissors. For example, companies like Johnson & Johnson use laser cutting to ensure sharp edges and intricate shapes necessary for medical procedures.
- Implants and Prosthetics: Laser cutting machines are employed to produce implants and prosthetics with exact dimensions and biocompatible materials. This includes dental implants, joint replacements, and orthopedic devices.
- Sterile Packaging: Laser cutting is used to create sterile packaging for medical devices, ensuring that the packaging is precise and free from contaminants.
Custom Metal Fabrication
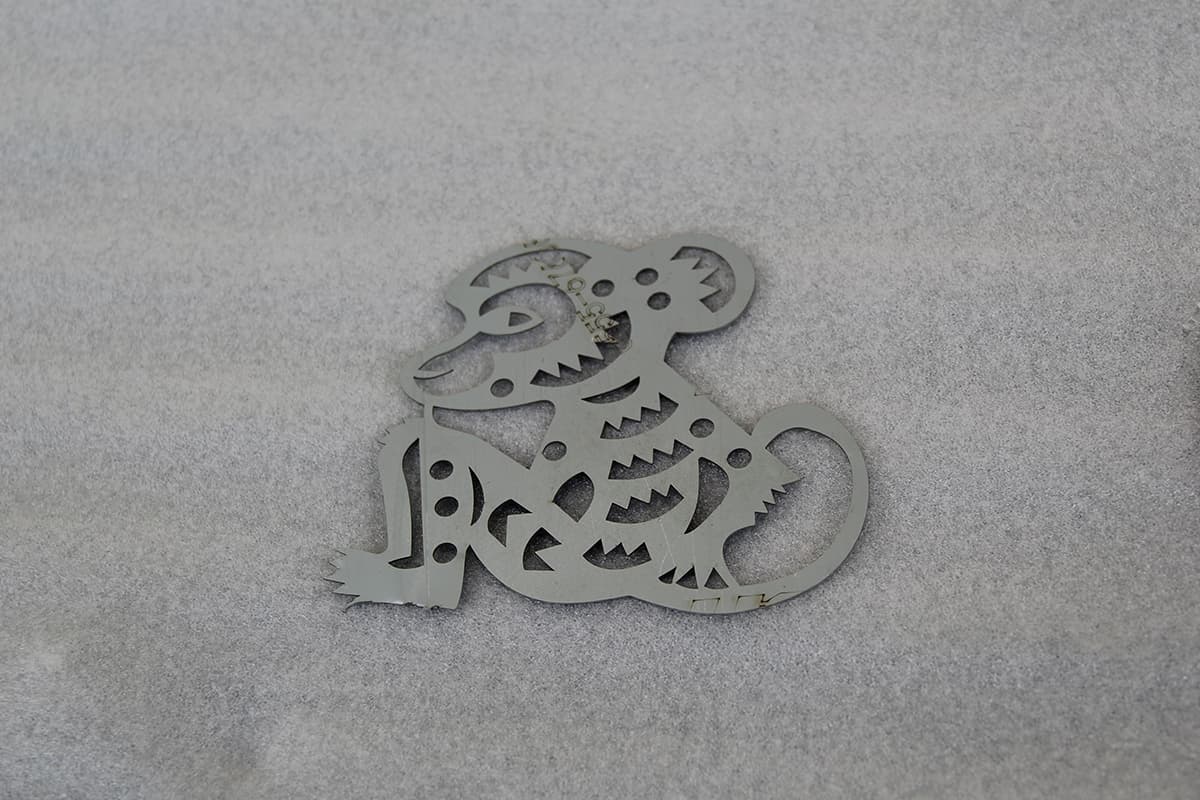
Laser cutting technology is widely used in custom metal fabrication due to its versatility and ability to handle various materials and thicknesses.
- Architectural Elements: Laser cutting is used to create custom architectural elements such as decorative panels, railings, and facades. The precision of laser cutting allows for intricate designs and patterns that add aesthetic value to buildings.
- Art and Sculpture: Artists and sculptors use laser cutting machines to create detailed and complex artworks from metal. The accuracy and flexibility of laser cutting enable artists to bring their creative visions to life.
- Prototyping and Small Batch Production: Laser cutting is ideal for prototyping and small batch production of custom metal parts. It allows for quick turnaround times and high precision, making it suitable for industries such as aerospace, automotive, and consumer products.
Future Trends in Laser Cutting Technology
The future of laser cutting technology looks promising, with advancements aimed at increasing efficiency, precision, and applications.
- Automation and AI Integration: Future laser cutting machines will increasingly integrate automation and artificial intelligence to optimize cutting paths, reduce waste, and enhance productivity.
- Enhanced Material Capabilities: Research and development are focusing on expanding the range of materials that can be efficiently cut by lasers, including advanced composites and new metal alloys.
- Improved Energy Efficiency: Innovations are being made to improve the energy efficiency of laser cutting machines, making them more sustainable and cost-effective.
- 3D Laser Cutting: The development of 3D laser cutting technology will allow for more complex geometries and multi-dimensional cutting, opening new possibilities in various industries.
V. FAQ
1. How does a fiber laser cutter differ from a CO2 laser cutter?
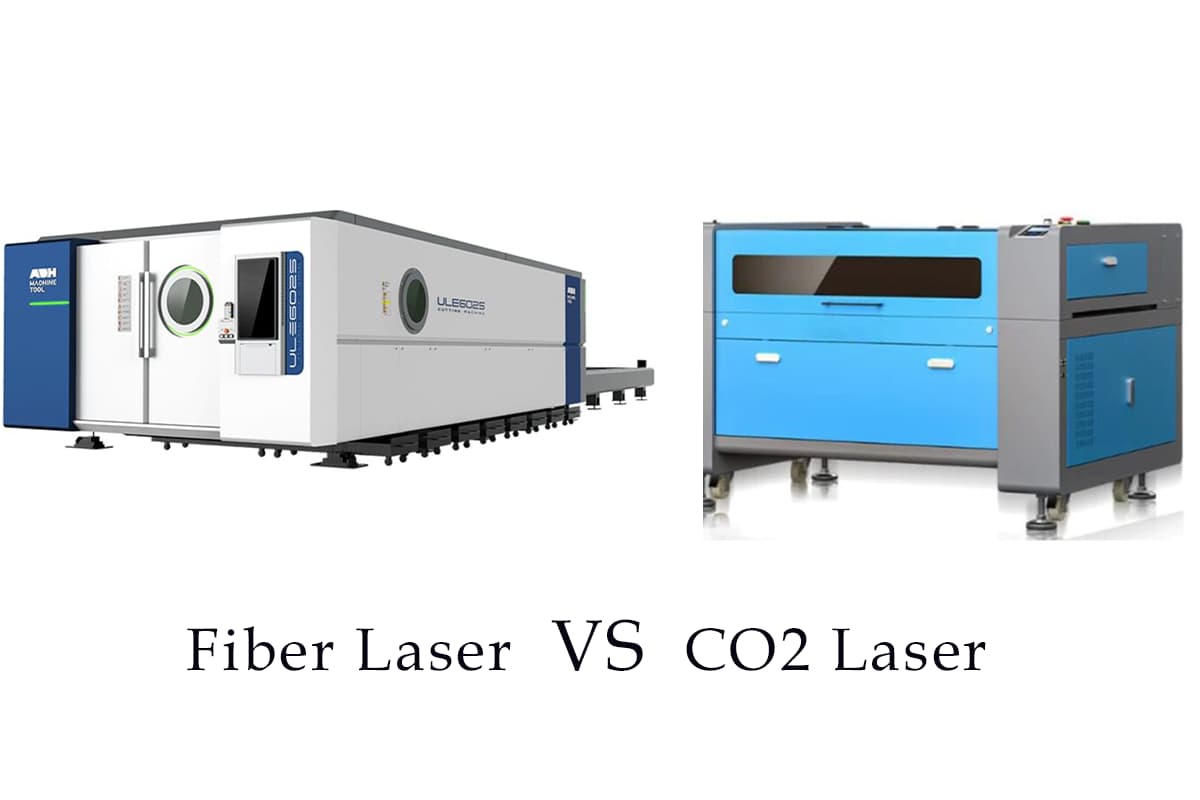
Fiber laser cutters and CO2 laser cutters differ primarily in their laser generation methods and their suitability for various materials. Fiber lasers use optical fibers doped with rare-earth elements to generate the laser beam, resulting in higher energy efficiency and faster cutting speeds, particularly for metals.
They are also better suited for cutting reflective metals like aluminum and copper. On the other hand, CO2 lasers generate the laser beam by electrically stimulating a gas mixture, making them ideal for cutting non-metal materials such as wood and acrylic.
2. What are the safety measures for operating laser-cutting machines?
Operating laser-cutting machines requires strict adherence to safety standards to prevent accidents and injuries. Key safety measures include wearing appropriate personal protective equipment (PPE) such as safety goggles that can filter the specific wavelength of the laser being used.
Operators should also ensure proper ventilation and use fume extraction systems to mitigate inhalation of harmful fumes and particulates. Additionally, regular maintenance and inspection of the machine, along with proper training for operators, are essential to ensure safe operation. Emergency stop buttons and interlock systems should always be functional and easily accessible.
3. Are there any limitations on the thickness of materials that can be cut?
Yes, there are limitations on the material thickness that laser cutting machines can handle, which vary depending on the type of laser used. CO2 lasers can generally cut non-metallic materials up to several inches thick but are less effective for thicker metals.
Fiber lasers excel in cutting thin to moderately thick metals, typically up to 1-inch thickness for stainless steel and aluminum. YAG lasers, although precise, are usually limited to thinner materials due to their lower power output. Beyond these thicknesses, other cutting methods such as plasma or waterjet cutting may be more suitable.
Telescoping Truck Mounted Crane
Mounted Truck Crane,Crane Truck Mounted,Unic Truck Mounted Crane
Hubei Chenglongwei Special Purpose Vehicle Co., Ltd. , https://www.clw-automobile.com