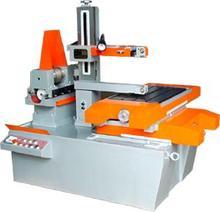
The locomotives for the first six times of China's railway speed increase are mainly DF11G diesel locomotives, which are mainly based on CSR vehicles. In the past two years, the speed of railways has been dominated by electric locomotives. However, diesel locomotives still have an irreplaceable position, especially in speeding freight locomotives. From the overall perspective, the demand for diesel locomotives is still quite large. There are currently more than 19,000 diesel locomotives in the whole country. In addition, large-capacity locomotive locomotives are currently in short supply in major locomotives, coal mines, and petroleum companies. According to preliminary estimates, the total number of locomotives to be updated every year is more than 600 (not Including about a few thousand repair vehicles each year).
I. Brief explanation of the difficulty in processing of main parts of rail transit involves rail transit machining. Relatively speaking, the main parts that are difficult to machine are the bogie sections of bogies and air-core axle bushes, and the key components of diesel engines. . Locomotive diesel engine main parts have complex structure, manufacturing precision, shape and position tolerances and surface roughness requirements (the accuracy index is mostly in the 5 to 7 grade, roughness Ra0.4 or so), requiring good interchangeability, such as the body, the crankshaft The main purpose of the connecting rod and cylinder head is to ensure that the locomotive has good reliability, high durability and high safety factor in high-speed operation.
Second, the main processing equipment with the shallow said that machining is by the car, milling, planing, boring, drilling, grinding and other basic processing methods, around the different products, and the same product different processing procedures, in the past people used a lot of traditional structure The single processing functions of lathes, milling machines, planers, boring machines, drilling machines, grinding machines and other common equipment. With the development of technology, the proportion of these common equipments has dropped dramatically. Instead, they are mainly numerically-controlled lathes, vertical and horizontal machining centers, which are mainly uniaxial and biaxial machining.
With the development of random bed accessories and in-depth research on related technologies, today's CNC machine tools have been dominated by flexible, compound, multi-axis linkage, high precision, and high speed. Such as multi-axis milling and milling center, boring and milling center, follow-type grinder and so on. The performance of the machine tool also features high-speed, high-efficiency machining and intelligence along with the development of tool materials and manufacturing technology, computer software technology, precision measurement technology, and rapid servo drag technology. In addition, in order to meet the user's demand for product production, various types of machine tools with mixed functions and mashup technologies are also produced. Such as: laser and milling (DMG) knead together; milling and grinding (Wollenberg) knead together and so on.
In recent years, in order to meet the evolving market demands, CSR has mainly added or imported domestic and imported vertical and horizontal machining centers (for parts: connecting rods, cylinder heads, etc.); gantry machining centers (for parts: body , frame, etc.); milling and milling machining center (for parts: camshaft, crankshaft); boring and milling machining center (for parts: holding axle box, etc.); special crankshaft, camshaft grinding machine, and vertical double grinding head grinder. The machining center has the advantages of small floor space, one device can reach four or five sets of equipment, high processing quality, high reliability, and small operator effort.
Still taking the crankshaft as an example, a turning and milling center has replaced machining functions such as turning, milling, drilling, expansion, and reaming that could be achieved by 6-7 machine tools in the past, including all the crankshaft journals, connecting rod necks, and cranks. Machining, flange hole machining, keyway machining, machining of tapped holes, machining of main oil holes and inclined oil holes, etc., reduce the number of mountings, improve the accuracy of the product, and greatly reduce the preparation preparation for trial production of new products. The machining flexibility of the machine tool is greatly enhanced; similarly, a crankshaft follower grinder replaces the original ordinary large-scale cylindrical grinder and the connecting rod-neck crankshaft grinder. One device has the effect of two grinders, and the footprint is only one. Bench grinder.
In addition, CNC online measurement also solves the measurement problems in previous machining. Marposs FENAR-L online diameter measuring device can control the precision of on-line product processing in real time and set out of automatic alarm.
At the same time, in the application of the tool, the precision of the knife is solved, the processing of unqualified products is avoided, and the processing efficiency is improved. Previous on-line measurement is that stop operators use vernier calipers or internal and external cards based on the operator's experience; senior workers (more than 6th level) are generally around 0.02mm, and now the tool set can be accurately measured to μm, and reliability It is also extremely high.
Third, the application of composite tools 80 years, the tools used in machining are mostly welding tools, a few non-standard tools - but also welded structure. At present, only a few are welding tools. Most of them are machine tools, forming tools and compound tools. Especially for cutting tools used in advanced equipment such as machining centers, 100% are standard machine tools and non-standard machine tools. However, the cost of tools is also quite expensive. (Tools consume 5 to 15% of the manufacturing cost.)
The composite processing technology realizes the relative concentration of processing procedures, reduces the number of repeated loading and unloading of the workpieces, positioning times, shortens the processing auxiliary time, improves the workpiece processing accuracy and production efficiency, and significantly reduces the number of equipment, saving the production area of ​​the production line and enabling the unit area. The output has been greatly increased, but at the same time it has also reduced the labor intensity of workers (on the other hand, it needs to improve the workers' cultural and technical qualities).
In addition, in the composite machining, it is quite common to use the formed composite cutter to process some holes with high concentricity or to process some complex shapes. One is because of the high precision and the second is the high processing efficiency. It is quite common in some high-end machining fields such as Europe and the United States. However, because there are still some gaps in manufacturing precision among Chinese tool manufacturers, they have not been promoted in the railway industry in recent years. This may be a weak link for future development.
Fourth, the insufficiency of the status quo and the problems to be solved by the tool holder: The tooling used by each machine tool factory is different, and the tool setting tool is also different. The cost of a single tool is 40 to 500,000, and even reaches millions; Cheaper than 3 to 5 million, there is no inconvenience to the tool processing, but each device is equipped with a knife instrument also brings additional burden on the user; in addition, the failure rate is also high. Often bad, repairs are also quite difficult. - This good thing has become a bad thing.
V. Actual use problems During the ordering of the machine tool, there was insufficient communication between the two parties on the process, leading to a long time span for pre-acceptance and final acceptance. After the inspection and acceptance, there were considerable details (programming, tool usage, and foreign Deviations in the understanding of drawings and processes, etc.).
Rail transit and machine tool manufacturing promote mutual development and common development The rapid development of rail transit has indeed brought new opportunities for development to the machine tool equipment industry and the corresponding tool industry. The 8th China International Metalworking Summit Forum was held in Nanjing in April 2012. The theme of this summit forum was “Towards an era of total solutionâ€, which triggered heated discussions among experts and scholars from all walks of life.
The current Chinese companies, after introducing advanced machine tool equipment and tools, combined with the special products of rail transit, have a long process of digestion, absorption and consolidation. Especially for process programming, operators, and even production management personnel, there is a gradual process from unfamiliarity to preliminary grasp to ease of application. Therefore, how to be a good company's technologist to help companies put their equipment and tools into use as quickly as possible and generate benefits quickly - this, in turn, sets a good image for their products. This is a new topic for equipment manufacturers. At the same time, how to quickly master advanced equipment technologies is also a lasting issue faced by Chinese and corporate customers.
The future development of rail transit manufacturing will continue to grow with the development of random bed manufacturing; it will continue to evolve with the different needs of all industries. Green and diversified (to meet the requirements of different users), low noise, low pollution, low fuel consumption, low emissions (to meet Tier IV emission requirements) and high reliability are also targets for the design and manufacture of diesel locomotives. CSR Qishuyan Locomotive Co., Ltd. plans to continue efforts in this direction through international cooperation.
Liquid Cold Plate,Liquid Cooling Plate,Water Cooling Plate,Water Cold Plate
Suzhou Wint Electric Co., Ltd , https://www.wintocool.com