I. INTRODUCTION The Yangzhou No. 2 Power Plant is a newly-built large-scale thermal power plant in Jiangsu Province. Two 600 MW units of the power plant were put into operation in August 1998 and 1999~4 respectively. Due to the poor manufacturing process, complex structure, low reliability, and frequent failures of the original SSC system, magnetic loss accidents have occurred more than two times. Excitation system problems have seriously threatened the safe operation of the unit. Therefore, under the joint efforts of our company and Yangzhou No.2 Power Plant, we have reconstructed part of the excitation system of No. 1 unit, and now the transformation of No. 2 unit is in progress. This article gives an introduction to this transformation.
Second, the basic situation of the system Yangzhou Second Power Plant unit capacity of 600MW, self-constant thyristor excitation, a total of 14 excitation system, including a regulator cabinet, 2 AC inlet cabinet, 2 AC switch cabinet , 1 DC outlet cabinet, 4 SCR bridge cabinets, 2 typhoon cabinets, 1 protection relay cabinet and 1 transmitter and insulation monitoring cabinet, excitation system produced by the United States Westinghouse, generator set and excitation parameters are as follows :
Rated capacity: 741MVA rated power: 600MW
Stator voltage: 20kV stator current: 21390A
Rated excitation power: 6337A rated excitation voltage: 513V
No-load excitation current: 2065A no-load excitation voltage; 167.168V
Maximum excitation current (continuous): 7000A maximum excitation voltage (continuous): 1250V
Third, the problem of excitation system analysis The excitation system of Yangzhou No.2 Power Plant has experienced many anomalies during the operation, resulting in a large range of reactive power fluctuations or switching to manual channel operation, which seriously threatens the safe operation of the unit. The main problem is concentrated in the excitation regulator.
The problems with the excitation regulator are analyzed as follows:
(1) The original regulator is equipped with dual automatic channels and single manual channels. When an automatic channel is running, the other automatic channel cannot be used. It can only be used as a cold backup. The two automatic channels are not hot standby and cannot be switched automatically. After the operation of the automatic channel failure, automatically cut to the manual channel, only to turn off the fault channel before they can start another automatic channel. This kind of automatic addition of a manual channel configuration can not meet the safety operation requirements of large-sized units such as 600MW in Yangzhou No. 2 Power Plant.
(2) The output of the regulator's automatic channel is the voltage regulation deviation signal of the machine terminal. The manual channel output is the rotor current regulation deviation signal. Both signals must be sent to the tracking module and the pulse forming module. In excitation adjustment, the tracking circuit is shared by the manual channel and the automatic channel. When the part fails, the excitation regulator cannot operate. Therefore, the automatic channel and the manual channel of the regulator are not completely independent channels and have a common part, and the reliability is not high.
(3) The pulse formation of the regulator is implemented by hardware circuits, and the hardware has four backups. The four circuits are all operated in parallel. One failure may affect the other three. The structure of the quad backup circuit is complex and is not conducive to Adjustment and maintenance.
(4) The anti-interference ability is poor, and the scene can not find the cause after several failures, and it often happens after recovery. According to Westinghouse technical personnel, it is an interference problem, but it cannot be handled. Running in such a state, the instability of the excitation system becomes a heart disease for operators.
(5) The fault is not detected, there is no alarm, the fault is not conducive to maintenance, there is no fault recorder after fault, and there is no useful data for fault analysis.
(6) The original regulator to save the setting data needs battery power, only need to replace the battery once in half a year, affecting the unit's safe operation.
To sum up, the regulator technology is backward, the structure is irrational, the operating mode is not flexible, the system hardware structure is complex, and the reliability is low.
Fourth, the transformation program instructions 1. Contents and Difficulty of Transformation The modification of the excitation system of the 600 MW unit of Yangzhou No. 2 Power Plant is to use NARI's SJ800(D) dual-microcomputer exciter regulator to replace the dual automatic channels of the original regulator while retaining the original manual channel.
The two automatic channels of the original regulator are all used, and the two channels of the SJ800(D) dual-microcomputer excitation regulator are replaced, and the manual channel of the original regulator is retained. After the excitation system is modified, there are two channels of the SJ800 (including two automatic channels and two manual channels) and one manual channel of the original regulator. After the transformation, the two channels of the SJ800 are normally operated. The A channel is used as the main channel, the B channel is used as the hot standby channel, and the original regulator's manual channel C is used as the backup channel. During operation, when the A channel fails, it is automatically Cut to B channel operation; if A fault, B then fault, cut to C operation; realize no disturbance in switching. In operation, it is also possible to perform a bumpless handover between the three channels A, B, and C.
The schematic diagram of the location of the transformed equipment is shown in Figure 1, in which the black box is the content of this transformation. The schematic diagram of the modified regulator system structure is shown in Figure 2, in which the virtual box contains new contents for this transformation.
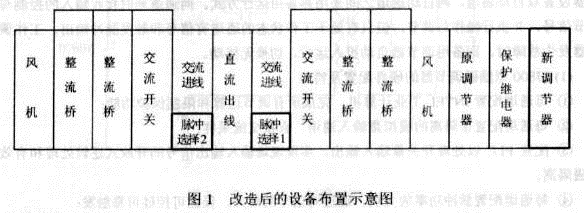
The difficulty of this program is twofold:
(1) The original manual channel is reserved. The pulse of the original manual channel cannot be changed. In order to realize the mutual switching between the automatic channel and the manual channel, the pulse of the automatic channel must be the same as the pulse of the manual channel, so we need to redesign the automatic channel. The pulse.
(2) If the original manual channel is reserved as a standby channel, the mutual tracking and mutual switching between the manual channel and the automatic channel must be solved.
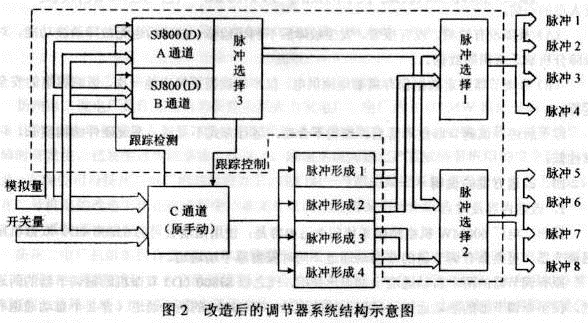
2. The SJ800(D) dual-microcomputer excitation regulator was used to modify the excitation of the 600MW turbogenerator in Yangzhou No. 2 Power Plant. We selected the SJ800(D) dual-microcomputer excitation regulator to update the original regulator. SJ800(D) Microcomputer Excitation Regulator is a dual-channel excitation regulator. It is based on INTEL industrial single board machine as the core, PLC logic processing, and intelligent regulators for large and medium-sized units. The integrated circuit in the regulator is 100% imported. The software has passed 95 percent of the tests of more than five years and nearly 100 units. The regulator is set to dual automatic channels, and hot standby operation is used between the two automatic channels. Both channels receive the input control and regulation signals at the same time, and perform operations and adjustments, but only the channels in the working state have signals and trigger pulses. When the working regulator fails, the standby regulator is automatically put into operation, and the switching is free from disturbance.
(1) Hardware configuration and features of SJ800 type excitation regulator 1 INTEL industrial computer is configured for each channel to complete all adjustment operations and limit protection functions;
2 Each channel is equipped with isolated analog input channels for direct ac sampling;
8 configure the PLC to handle digital input and output, open field logic input and output signal processing and effective electromagnetic isolation;
4 Each channel is equipped with a pulse power amplifier board to ensure reliable triggering of the SCR through amplification of the signal;
5 Configure a switch board for each channel to ensure physical isolation between the two channels and ensure reliable switchover during faults.
(2) The function of the excitation regulator 1 Regulation law: PID control mode + PSS.
2 operating mode: constant voltage closed-loop loop; constant rotor current closed loop mode.
3 Auxiliary and Excitation Limit Functions: Under-excitation instantaneous limit; Over-excitation delay limit; Strong excitation inverse time limit; V/F limit; PT disconnection detection and protection function; no-load over-voltage limit; dual-machine mutual tracking and no disturbance Switching; pulse loss and pulse anomaly detection functions; operating supply voltage monitoring and WatchDog function.
4 advanced functions: fault-tolerant control; failure of the excitation system record and power waveform recording; intelligent debugging, maintenance and test software functions and interfaces.
5 Self-test and self-diagnosis output: The self-test and self-diagnosis output are designed as two levels, the first level is the alarm; the second level is the switch to the alternate channel.
3. Excitation Regulator Pulse Design and Pulse Switching with the Original Manual Channel
(1) Pulse circuit design The pulse diagram of the original excitation system is shown in Fig. 3. The AC 60V power supply charges the pulse storage capacitor. The charge end voltage reaches 60√2 VV. When the pulse is generated, the circuit discharges the capacitor discharge, resulting in a peak. Up to 60√2̄V pulses.
The schematic diagram of the pulse triggering of the modified excitation regulator is shown in Fig. 4. The circuit has no stored charging capacitor and the pulse is directly powered by the pulsed power supply.
After simulation analysis and matching parameters, the new regulator pulse trigger energy is equivalent to the trigger energy of the original manual link, so as to ensure the reliability of the pulse trigger.
(2) Automatic/manual switching device The automatic/manual switching device adopts the relay switching control mode, which connects the automatic/manual and six-way pulse to the switching relay contacts respectively. The control relays are divided and controlled to control the thyristor trigger pulse signal. At the same time, an automatic/manual working signal is transmitted to the excitation system.
4. Mutual tracking and switching between automatic channels and manual channels (1) Control principle of manual channels (M300) Since Westinghouse did not provide a detailed explanation of the manual channels, we can only analyze them based on the schematic provided. M300 manual control device adopts current closed loop method for excitation adjustment, M300 measures the rotor current of the generator, and calculates the difference between the rotor current measurement value and the given value, and then outputs the trigger pulse after calculation by the operational amplifier. The angle of the trigger pulse and the rotor current are given. The value and the difference between the measured value and the given value are correlated so as to maintain the balance of the generator rotor current and the given value.
(2) Manual channel tracking The FCM signal response of the automatic channel M300 is the difference between the current reference value of the manual link and the actual current measurement value. The M300 FCM signal is sent to the automatic excitation regulator. The regulator determines whether the manual output and the automatic output are balanced by detecting the MCM FCM port level. When the value is near zero, it is balanced; when the value is positive or negative, the manual output is small or large, which is unbalanced. At this time, the regulator sends a command to increase or decrease the manual M300 and adjust the manual set value. Finally, the measured value of the manual link is equal to the given value. In this way, the manual link can accurately track the excitation current of the automatic channel operation. If switching from automatic to manual, the switching is basically non-disturbing.
(3) Automatic channel tracking Manual channel manual channel work, automatic regulator automatically track rotor current, automatic channel measurement of excitation current value, according to the preset excitation current and trigger angle relationship table, check the corresponding working angle, and set simultaneously The given value is the current measurement. In this way, the conditions of the automatic channel are basically equivalent to the current actual conditions. If automatic cutting is done by hand, the switching is basically free of disturbances.
V. Field trials after transformation The following field tests were performed on the retrofitted system:
Test at no-load, Short-circuit up-current test of the system, Zero-lift boost test of the regulator and pressure regulation range test, Step-up pressure test, Step response test, Inverter deactivation test, Auto-boost test, Switching test, Frequency Characteristics and V/F limit test.
Load test: grid-connected test; under-excitation test; over-excitation test; current closed-loop test; A, B sets of switching test; adjustment coefficient test.
Examples are described below.
1. No-load step response test Increase generator terminal voltage to rated value (100% UFN), type "TSTEP" command through the computer, make a ± 10% UFN step response test, observe the regulation performance, modify the PID parameters, and finally select A set of parameters: Kp=0FOH, KI=0080H, KD=02H. The dynamic response parameters of the generator are obtained from the ±10 % step response test oscillogram under this parameter (see the following table). The response parameter indicates that the regulator has good regulation performance.
2. The no-load inverter demagnetization test will adjust the terminal voltage to 100% UFN, set the “manual inverter†handle on the device's operation panel to the “cast†position, and the generator will be deactivated by inverter inversion, and the terminal voltage will automatically drop to zero. As can be seen from the oscillogram, the device has a stable inverter.
3. The no-load automatic boost test sets the operating handle on the device's operation panel to the "cut" position. Satisfy the conditions for starting the excitation, the generator automatically builds the voltage and stops when the voltage at the terminal automatically rises to 90% of the no-load rated voltage.
4. No-load switching test voltage is switched between closed-loop and current-closed loop, the voltage of the terminal does not fluctuate in the process of switching; A-set and B-set are switched to each other, the voltage of the terminal does not fluctuate during switching, and the switch between automatic and manual is performed. During the switching process, the terminal voltage is basically free of fluctuations. The test shows that the device solves the problems of mutual tracking and switching between the automatic channel of the new equipment and the manual channel of the old equipment, and ensures the mutual backup relationship between the two.
5. The no-load frequency characteristics and V/F limit test reduce the generator voltage frequency by adjusting the turbine speed. When the frequency is above 48.5Hz, the setpoint value of the generator voltage will remain unchanged, and the generator voltage will remain unchanged at the given value; when the frequency drops below 48.5Hz, the voltage setpoint of the generator will automatically decrease. The generator voltage drops below the setpoint, ensuring that the field current does not rise in the process; when the frequency drops to 45Hz, the regulator automatically de-excites the magnet. The test record is as follows:
The test shows that when the speed of the regulator is reduced under the no-load condition of the generator, the V/P limit acts correctly, and the terminal voltage is automatically reduced to effectively avoid the occurrence of low frequency overcurrent.
6. The undershoot curve of the load under-excitation test is based on the data given by the manufacturer. After the generator is connected to the grid, since there is no under-excitation test condition (the terminal voltage is too low), the user agrees to change the under-excitation action value to -50 MVAR and conduct the test. Adjust the generator reactive power to -51.0MVAR, adjust the device under-excitation instantaneous action, the under-excited indicator light, reactive value back to the phase-44.0MVAR, no longer change. At this time demagnetization, the generator reactive power unchanged.
7. The load overexcitation test was changed to test the generator over-excitation curve to 100MW, and the generator reactive power was adjusted to Q=110.00MVAR. After about 20 seconds, the regulator over-excitation limit action, the over-excitation indicator light, the reactive value callback, and the stability Q =90.31MVAR, no longer change. At this point, the magnetization is increased and the reactive power is not changed
8. The load switching test regulator is switched between A and B sets. The reactive power of the unit does not change during the switching process; the switching between the automatic excitation regulator and the manual channel is performed, and the reactive power of the unit does not change during the switching process.
6. Deep-in phase test From September 21, 2000 to September 22, 2000, unit No. 1 of the Yangzhou No. 2 Power Plant was required by the East China General Survey. To test the ability to enter the phase operation, the unit conducted a deep-in phase test. In order to ensure the safe operation of the unit during the test, the regulator always operates in the automatic state, the under-excitation limit is always input, and the regulator works normally during the test, creating conditions for the smooth running of the test.
1. The test content is done in three conditions of unit power of 600MW, 450MW, and 300MW to make the unit phase test.
2. During the test of the excitation system, the automatic excitation regulator is put into operation, and the under-excitation limit curve is set differently depending on the test depth, and the under-excitation restriction is put into operation.
3. Test conditions (1) P = 600MW, Q = -180MVAR Leading phase test The undershoot limit curve is adjusted to a straight line from (0, -270) to (600, -200). The regulator operates normally, the excitation ammeter is stable, the voltmeter is stable, and the test time is two hours.
(2) P = 450MW, Q = -200MVAR The undershoot limit curve of the incoming phase test is adjusted to a straight line from (0, -270) to (600, -220). The regulator operates normally, the excitation ammeter is stable, the voltmeter is stable, and the test time is two hours.
In the test, reactive power has fluctuations of 10 to 20 MVAR. The dead zone of the original PID regulation was reduced from ±3 yards to ±1 yard, and after the negative balance was reduced to -1%, the reactive power fluctuation range was reduced to 3 to 5 MVAR, and the excitation system was stable.
(3) P = 300MW, Q = -250MVAR The phase test undershoot test curve is adjusted to the (0MW, -280MVAR) to (600MW, -280MVAR) line. The regulator operates normally, the excitation current is stable, the voltage at the terminal is stable, and the reactive power fluctuation amplitude is 3MVAR. Before the start of this experiment, the PID adjustment dead zone was changed from ±4 yards to ±1 yards, and the negative balance was cancelled.
4. Test conclusion The test results prove that the microcomputer excitation regulator can meet the requirements of the phase operation of the No. 1 unit 600MW unit in Yangzhou No. 2 Power Plant. In order to better adapt the operating conditions of the phase-in operation, before the formal phase-in operation, the under-excitation curve of the phase-in operation has been modified, and the regulator parameters have been adjusted at the same time.
7. Conclusion The reform of the self-energizing magnetic system of the 600MW turbo-generator set in the Yangzhou No. 2 Power Plant is the first time the domestic excitation equipment has been used to reform the self-energizing magnetic system of the 600MW unit. The modified system can adapt to various operating conditions of the unit, including phase-in operation and deep-in-phase test conditions. This transformation, on the one hand, successfully introduced the new regulation system, and on the other hand successfully solved the problem of interface and coordination between the old and new equipment. The adjustment performance of the new adjustment system has greatly improved the quality of the original equipment; the reliability of the system after the transformation has also been greatly improved compared with the original equipment. By April 1, 2001, it has been operating safely and stably for 10 months. The successful transformation of the self-energizing magnetic system of the 600MW turbo-generator unit in the Yangzhou No. 2 Power Plant indicates that the domestic excitation technology level is fully capable of providing the transformation or new excitation equipment for the ultra-large unit.
Second, the basic situation of the system Yangzhou Second Power Plant unit capacity of 600MW, self-constant thyristor excitation, a total of 14 excitation system, including a regulator cabinet, 2 AC inlet cabinet, 2 AC switch cabinet , 1 DC outlet cabinet, 4 SCR bridge cabinets, 2 typhoon cabinets, 1 protection relay cabinet and 1 transmitter and insulation monitoring cabinet, excitation system produced by the United States Westinghouse, generator set and excitation parameters are as follows :
Rated capacity: 741MVA rated power: 600MW
Stator voltage: 20kV stator current: 21390A
Rated excitation power: 6337A rated excitation voltage: 513V
No-load excitation current: 2065A no-load excitation voltage; 167.168V
Maximum excitation current (continuous): 7000A maximum excitation voltage (continuous): 1250V
Third, the problem of excitation system analysis The excitation system of Yangzhou No.2 Power Plant has experienced many anomalies during the operation, resulting in a large range of reactive power fluctuations or switching to manual channel operation, which seriously threatens the safe operation of the unit. The main problem is concentrated in the excitation regulator.
The problems with the excitation regulator are analyzed as follows:
(1) The original regulator is equipped with dual automatic channels and single manual channels. When an automatic channel is running, the other automatic channel cannot be used. It can only be used as a cold backup. The two automatic channels are not hot standby and cannot be switched automatically. After the operation of the automatic channel failure, automatically cut to the manual channel, only to turn off the fault channel before they can start another automatic channel. This kind of automatic addition of a manual channel configuration can not meet the safety operation requirements of large-sized units such as 600MW in Yangzhou No. 2 Power Plant.
(2) The output of the regulator's automatic channel is the voltage regulation deviation signal of the machine terminal. The manual channel output is the rotor current regulation deviation signal. Both signals must be sent to the tracking module and the pulse forming module. In excitation adjustment, the tracking circuit is shared by the manual channel and the automatic channel. When the part fails, the excitation regulator cannot operate. Therefore, the automatic channel and the manual channel of the regulator are not completely independent channels and have a common part, and the reliability is not high.
(3) The pulse formation of the regulator is implemented by hardware circuits, and the hardware has four backups. The four circuits are all operated in parallel. One failure may affect the other three. The structure of the quad backup circuit is complex and is not conducive to Adjustment and maintenance.
(4) The anti-interference ability is poor, and the scene can not find the cause after several failures, and it often happens after recovery. According to Westinghouse technical personnel, it is an interference problem, but it cannot be handled. Running in such a state, the instability of the excitation system becomes a heart disease for operators.
(5) The fault is not detected, there is no alarm, the fault is not conducive to maintenance, there is no fault recorder after fault, and there is no useful data for fault analysis.
(6) The original regulator to save the setting data needs battery power, only need to replace the battery once in half a year, affecting the unit's safe operation.
To sum up, the regulator technology is backward, the structure is irrational, the operating mode is not flexible, the system hardware structure is complex, and the reliability is low.
Fourth, the transformation program instructions 1. Contents and Difficulty of Transformation The modification of the excitation system of the 600 MW unit of Yangzhou No. 2 Power Plant is to use NARI's SJ800(D) dual-microcomputer exciter regulator to replace the dual automatic channels of the original regulator while retaining the original manual channel.
The two automatic channels of the original regulator are all used, and the two channels of the SJ800(D) dual-microcomputer excitation regulator are replaced, and the manual channel of the original regulator is retained. After the excitation system is modified, there are two channels of the SJ800 (including two automatic channels and two manual channels) and one manual channel of the original regulator. After the transformation, the two channels of the SJ800 are normally operated. The A channel is used as the main channel, the B channel is used as the hot standby channel, and the original regulator's manual channel C is used as the backup channel. During operation, when the A channel fails, it is automatically Cut to B channel operation; if A fault, B then fault, cut to C operation; realize no disturbance in switching. In operation, it is also possible to perform a bumpless handover between the three channels A, B, and C.
The schematic diagram of the location of the transformed equipment is shown in Figure 1, in which the black box is the content of this transformation. The schematic diagram of the modified regulator system structure is shown in Figure 2, in which the virtual box contains new contents for this transformation.
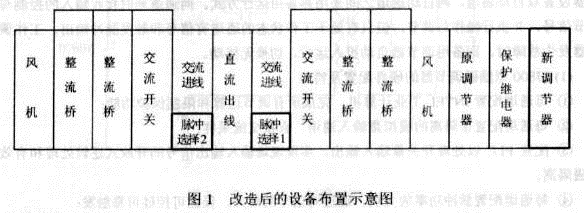
The difficulty of this program is twofold:
(1) The original manual channel is reserved. The pulse of the original manual channel cannot be changed. In order to realize the mutual switching between the automatic channel and the manual channel, the pulse of the automatic channel must be the same as the pulse of the manual channel, so we need to redesign the automatic channel. The pulse.
(2) If the original manual channel is reserved as a standby channel, the mutual tracking and mutual switching between the manual channel and the automatic channel must be solved.
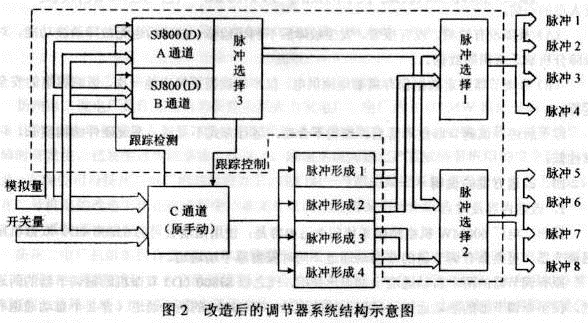
2. The SJ800(D) dual-microcomputer excitation regulator was used to modify the excitation of the 600MW turbogenerator in Yangzhou No. 2 Power Plant. We selected the SJ800(D) dual-microcomputer excitation regulator to update the original regulator. SJ800(D) Microcomputer Excitation Regulator is a dual-channel excitation regulator. It is based on INTEL industrial single board machine as the core, PLC logic processing, and intelligent regulators for large and medium-sized units. The integrated circuit in the regulator is 100% imported. The software has passed 95 percent of the tests of more than five years and nearly 100 units. The regulator is set to dual automatic channels, and hot standby operation is used between the two automatic channels. Both channels receive the input control and regulation signals at the same time, and perform operations and adjustments, but only the channels in the working state have signals and trigger pulses. When the working regulator fails, the standby regulator is automatically put into operation, and the switching is free from disturbance.
(1) Hardware configuration and features of SJ800 type excitation regulator 1 INTEL industrial computer is configured for each channel to complete all adjustment operations and limit protection functions;
2 Each channel is equipped with isolated analog input channels for direct ac sampling;
8 configure the PLC to handle digital input and output, open field logic input and output signal processing and effective electromagnetic isolation;
4 Each channel is equipped with a pulse power amplifier board to ensure reliable triggering of the SCR through amplification of the signal;
5 Configure a switch board for each channel to ensure physical isolation between the two channels and ensure reliable switchover during faults.
(2) The function of the excitation regulator 1 Regulation law: PID control mode + PSS.
2 operating mode: constant voltage closed-loop loop; constant rotor current closed loop mode.
3 Auxiliary and Excitation Limit Functions: Under-excitation instantaneous limit; Over-excitation delay limit; Strong excitation inverse time limit; V/F limit; PT disconnection detection and protection function; no-load over-voltage limit; dual-machine mutual tracking and no disturbance Switching; pulse loss and pulse anomaly detection functions; operating supply voltage monitoring and WatchDog function.
4 advanced functions: fault-tolerant control; failure of the excitation system record and power waveform recording; intelligent debugging, maintenance and test software functions and interfaces.
5 Self-test and self-diagnosis output: The self-test and self-diagnosis output are designed as two levels, the first level is the alarm; the second level is the switch to the alternate channel.
3. Excitation Regulator Pulse Design and Pulse Switching with the Original Manual Channel
(1) Pulse circuit design The pulse diagram of the original excitation system is shown in Fig. 3. The AC 60V power supply charges the pulse storage capacitor. The charge end voltage reaches 60√2 VV. When the pulse is generated, the circuit discharges the capacitor discharge, resulting in a peak. Up to 60√2̄V pulses.
The schematic diagram of the pulse triggering of the modified excitation regulator is shown in Fig. 4. The circuit has no stored charging capacitor and the pulse is directly powered by the pulsed power supply.
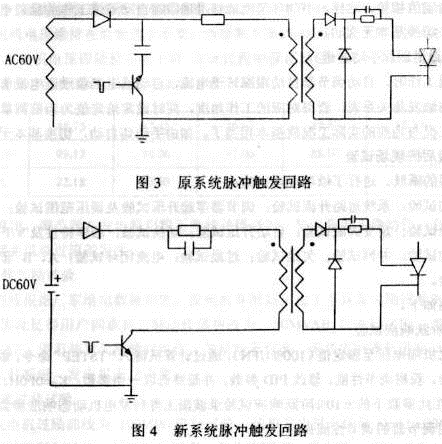
(2) Automatic/manual switching device The automatic/manual switching device adopts the relay switching control mode, which connects the automatic/manual and six-way pulse to the switching relay contacts respectively. The control relays are divided and controlled to control the thyristor trigger pulse signal. At the same time, an automatic/manual working signal is transmitted to the excitation system.
4. Mutual tracking and switching between automatic channels and manual channels (1) Control principle of manual channels (M300) Since Westinghouse did not provide a detailed explanation of the manual channels, we can only analyze them based on the schematic provided. M300 manual control device adopts current closed loop method for excitation adjustment, M300 measures the rotor current of the generator, and calculates the difference between the rotor current measurement value and the given value, and then outputs the trigger pulse after calculation by the operational amplifier. The angle of the trigger pulse and the rotor current are given. The value and the difference between the measured value and the given value are correlated so as to maintain the balance of the generator rotor current and the given value.
(2) Manual channel tracking The FCM signal response of the automatic channel M300 is the difference between the current reference value of the manual link and the actual current measurement value. The M300 FCM signal is sent to the automatic excitation regulator. The regulator determines whether the manual output and the automatic output are balanced by detecting the MCM FCM port level. When the value is near zero, it is balanced; when the value is positive or negative, the manual output is small or large, which is unbalanced. At this time, the regulator sends a command to increase or decrease the manual M300 and adjust the manual set value. Finally, the measured value of the manual link is equal to the given value. In this way, the manual link can accurately track the excitation current of the automatic channel operation. If switching from automatic to manual, the switching is basically non-disturbing.
(3) Automatic channel tracking Manual channel manual channel work, automatic regulator automatically track rotor current, automatic channel measurement of excitation current value, according to the preset excitation current and trigger angle relationship table, check the corresponding working angle, and set simultaneously The given value is the current measurement. In this way, the conditions of the automatic channel are basically equivalent to the current actual conditions. If automatic cutting is done by hand, the switching is basically free of disturbances.
V. Field trials after transformation The following field tests were performed on the retrofitted system:
Test at no-load, Short-circuit up-current test of the system, Zero-lift boost test of the regulator and pressure regulation range test, Step-up pressure test, Step response test, Inverter deactivation test, Auto-boost test, Switching test, Frequency Characteristics and V/F limit test.
Load test: grid-connected test; under-excitation test; over-excitation test; current closed-loop test; A, B sets of switching test; adjustment coefficient test.
Examples are described below.
1. No-load step response test Increase generator terminal voltage to rated value (100% UFN), type "TSTEP" command through the computer, make a ± 10% UFN step response test, observe the regulation performance, modify the PID parameters, and finally select A set of parameters: Kp=0FOH, KI=0080H, KD=02H. The dynamic response parameters of the generator are obtained from the ±10 % step response test oscillogram under this parameter (see the following table). The response parameter indicates that the regulator has good regulation performance.

2. The no-load inverter demagnetization test will adjust the terminal voltage to 100% UFN, set the “manual inverter†handle on the device's operation panel to the “cast†position, and the generator will be deactivated by inverter inversion, and the terminal voltage will automatically drop to zero. As can be seen from the oscillogram, the device has a stable inverter.
3. The no-load automatic boost test sets the operating handle on the device's operation panel to the "cut" position. Satisfy the conditions for starting the excitation, the generator automatically builds the voltage and stops when the voltage at the terminal automatically rises to 90% of the no-load rated voltage.
4. No-load switching test voltage is switched between closed-loop and current-closed loop, the voltage of the terminal does not fluctuate in the process of switching; A-set and B-set are switched to each other, the voltage of the terminal does not fluctuate during switching, and the switch between automatic and manual is performed. During the switching process, the terminal voltage is basically free of fluctuations. The test shows that the device solves the problems of mutual tracking and switching between the automatic channel of the new equipment and the manual channel of the old equipment, and ensures the mutual backup relationship between the two.
5. The no-load frequency characteristics and V/F limit test reduce the generator voltage frequency by adjusting the turbine speed. When the frequency is above 48.5Hz, the setpoint value of the generator voltage will remain unchanged, and the generator voltage will remain unchanged at the given value; when the frequency drops below 48.5Hz, the voltage setpoint of the generator will automatically decrease. The generator voltage drops below the setpoint, ensuring that the field current does not rise in the process; when the frequency drops to 45Hz, the regulator automatically de-excites the magnet. The test record is as follows:

The test shows that when the speed of the regulator is reduced under the no-load condition of the generator, the V/P limit acts correctly, and the terminal voltage is automatically reduced to effectively avoid the occurrence of low frequency overcurrent.
6. The undershoot curve of the load under-excitation test is based on the data given by the manufacturer. After the generator is connected to the grid, since there is no under-excitation test condition (the terminal voltage is too low), the user agrees to change the under-excitation action value to -50 MVAR and conduct the test. Adjust the generator reactive power to -51.0MVAR, adjust the device under-excitation instantaneous action, the under-excited indicator light, reactive value back to the phase-44.0MVAR, no longer change. At this time demagnetization, the generator reactive power unchanged.
7. The load overexcitation test was changed to test the generator over-excitation curve to 100MW, and the generator reactive power was adjusted to Q=110.00MVAR. After about 20 seconds, the regulator over-excitation limit action, the over-excitation indicator light, the reactive value callback, and the stability Q =90.31MVAR, no longer change. At this point, the magnetization is increased and the reactive power is not changed
8. The load switching test regulator is switched between A and B sets. The reactive power of the unit does not change during the switching process; the switching between the automatic excitation regulator and the manual channel is performed, and the reactive power of the unit does not change during the switching process.
6. Deep-in phase test From September 21, 2000 to September 22, 2000, unit No. 1 of the Yangzhou No. 2 Power Plant was required by the East China General Survey. To test the ability to enter the phase operation, the unit conducted a deep-in phase test. In order to ensure the safe operation of the unit during the test, the regulator always operates in the automatic state, the under-excitation limit is always input, and the regulator works normally during the test, creating conditions for the smooth running of the test.
1. The test content is done in three conditions of unit power of 600MW, 450MW, and 300MW to make the unit phase test.
2. During the test of the excitation system, the automatic excitation regulator is put into operation, and the under-excitation limit curve is set differently depending on the test depth, and the under-excitation restriction is put into operation.
3. Test conditions (1) P = 600MW, Q = -180MVAR Leading phase test The undershoot limit curve is adjusted to a straight line from (0, -270) to (600, -200). The regulator operates normally, the excitation ammeter is stable, the voltmeter is stable, and the test time is two hours.
(2) P = 450MW, Q = -200MVAR The undershoot limit curve of the incoming phase test is adjusted to a straight line from (0, -270) to (600, -220). The regulator operates normally, the excitation ammeter is stable, the voltmeter is stable, and the test time is two hours.
In the test, reactive power has fluctuations of 10 to 20 MVAR. The dead zone of the original PID regulation was reduced from ±3 yards to ±1 yard, and after the negative balance was reduced to -1%, the reactive power fluctuation range was reduced to 3 to 5 MVAR, and the excitation system was stable.
(3) P = 300MW, Q = -250MVAR The phase test undershoot test curve is adjusted to the (0MW, -280MVAR) to (600MW, -280MVAR) line. The regulator operates normally, the excitation current is stable, the voltage at the terminal is stable, and the reactive power fluctuation amplitude is 3MVAR. Before the start of this experiment, the PID adjustment dead zone was changed from ±4 yards to ±1 yards, and the negative balance was cancelled.
4. Test conclusion The test results prove that the microcomputer excitation regulator can meet the requirements of the phase operation of the No. 1 unit 600MW unit in Yangzhou No. 2 Power Plant. In order to better adapt the operating conditions of the phase-in operation, before the formal phase-in operation, the under-excitation curve of the phase-in operation has been modified, and the regulator parameters have been adjusted at the same time.
7. Conclusion The reform of the self-energizing magnetic system of the 600MW turbo-generator set in the Yangzhou No. 2 Power Plant is the first time the domestic excitation equipment has been used to reform the self-energizing magnetic system of the 600MW unit. The modified system can adapt to various operating conditions of the unit, including phase-in operation and deep-in-phase test conditions. This transformation, on the one hand, successfully introduced the new regulation system, and on the other hand successfully solved the problem of interface and coordination between the old and new equipment. The adjustment performance of the new adjustment system has greatly improved the quality of the original equipment; the reliability of the system after the transformation has also been greatly improved compared with the original equipment. By April 1, 2001, it has been operating safely and stably for 10 months. The successful transformation of the self-energizing magnetic system of the 600MW turbo-generator unit in the Yangzhou No. 2 Power Plant indicates that the domestic excitation technology level is fully capable of providing the transformation or new excitation equipment for the ultra-large unit.
Fitness Accessories,Home Fit Equip,Gym Waist Trimmer,Gym Fitness Accessories
Hangzhou Gymbo Sports Co., Ltd , https://www.gymbosports.com