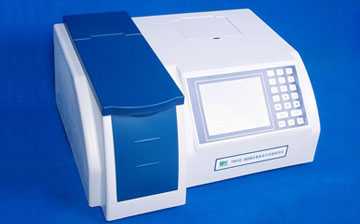
At the same time, the state requires companies to assume the main responsibility for quality inspection, and the corresponding companies are also willing to improve safety inspection standards and improve the image of the company and the industry in order to avoid or reduce the impact of food safety incidents. Leading companies in the industry have taken control of upstream raw material control and testing as the focus of improvement and have invested heavily in both areas.
At present, China has more than 23,000 inspection agencies, including agricultural inspection and quarantine stations, disease control centers, product quality supervision and inspection stations, station inspection and quarantine bureaus, and various types of environmental monitoring stations, and more than 400,000 food processing companies.
The research team pointed out that the cost of purchasing equipment for food companies to meet product testing is about 1 million yuan, and the cost of testing equipment for testing organizations is about 15 to 30 million yuan.
In the future, the potential market for analytical instruments in the field of food safety testing in China will be over 704 billion yuan, of which food processing companies will have a market equivalent of 400 billion, and testing organizations will have 345 billion, and the demand for consumables will not be counted.
China is a major producer, consumer, and exporter of agricultural products and foods. Currently, it has more than 400,000 food processing companies of all kinds. Today, as the public increasingly pays attention to food safety issues, it is destined that the potential market for food safety testing instruments will be very high in the future. huge.
As a core force in detection technology R&D, food safety monitoring instrument manufacturers are indispensable to increase scientific research and actively break through existing detection technologies; however, from a business perspective, he is different from a public interest organization and does not need to be profitable. As a company, profitability is the fundamental purpose. Therefore, as a food safety inspection instrument manufacturing company, testing technology and corporate profitability, are the two most important considerations. This article mainly from the perspective of profitability, combined with the profitability of some typical enterprises in the domestic and foreign industries, a simple comparative analysis of the profit model of food safety testing instrument manufacturers.
The first is the analysis of the profit model of food safety testing equipment manufacturers.
According to the position of the company's business in the industry chain, the current industry of food safety inspection instrument companies mainly has the following two profit models: One is the simple product design, production and sales with technology as the core, mainly the production standard testing equipment and its supporting equipment. enterprise. At present, most domestic companies fall into this category. The other is to provide a complete solution based on customer needs, not only to provide products, but also to provide related services related to product support, including personalized product design, configuration and perfect after-sales service.
Secondly, a comparative analysis was conducted on the profit models of typical enterprises manufacturing food safety testing instruments.
From an international perspective, the leading international food safety testing equipment manufacturers can not only provide advanced testing equipment, but also provide complete solutions including thoughtful pre-sales and after-sales services. The source of their profits is also mainly from the "products." And the "service" two major components. Taking Agilent and ThermoFisher as examples: In 2011, Agilent’s gross profit composition accounted for 14.74% of service items; ThermoFisher’s service projects accounted for 13.12% of the company’s total gross profit.
Among domestic enterprises, gaining the benefits of “standard testing equipment and its supporting production and sales†remains the profit model of most manufacturers of food safety testing instruments. Taking "Tianrui Instrument (300165)" as an example, the company's annual report data shows that the company's gross profit in 2011 mainly comes from energy dispersive XRF, wavelength dispersion XRF, and sales of other inspection products, among which energy dispersive XRF and wavelength dispersion XRF together account for the company. Gross profit for the year was 92.77%. From the perspective of company operations, in 2011, the company’s operating profit accounted for 73.76% of total profits, and non-operating profits accounted for 26.24%. In recent years, the proportion of non-operating profits increased year by year.
Comparing the profits of the above-mentioned industry leaders at home and abroad, the Food Safety Monitoring Equipment Manufacturing Industry Research Group of the Industry Research Institute of Qianfeng Research Institute believes that, from a comprehensive point of view, the profitability of the service projects of the domestic domestic enterprises is relatively large and urgently needed to be developed. Should see this, make full use of this profit space, as soon as possible to adjust the corporate profit model, to the overall solution model direction transformation and upgrading.
As a major force in improving the level of food safety monitoring, it is incumbent on food safety testing equipment manufacturers to vigorously develop R&D to improve the detection technology. It is necessary to strive to improve the level of detection and thus improve the overall profitability. At the same time, the company acts as a profit-oriented company. Legal person, profitability is the fundamental of survival. Industry companies should actively pay attention to changes in the profit space in the industry, seize the opportunity, actively adjust their own strategies and profit models, and comprehensively enhance their competitiveness.
Sheet Metal Fabrication
Definition of sheet metal fabrication
Sheet Metal fabrication is the creation of useful metallic parts and structures by the application of multiple fabrication processes. Sheet metal fabrication is basically a broad term that involves various complex processes like cutting, forming, bending, welding, machining, and assembling. The instructions include below: materials, processes, and tools required for sheet metal fabrication.
Types of Sheet Metal Fabrication Materials
The choice of metal depends on the final use of the fabricated parts.
Common fabrication processes:
· Carbon Steel
· Stainless Steel
· Aluminum
· Bronze
· Copper
· Brass
· Aluminized steel
· Galvanized steel
Types of Metal Fabrication Processes
The journey to the final product from raw sheet metals proceeds through various sheet metal fabrication processes. All the sheet metal fabrication processes can be grouped into the following three categories:
· Cutting
· Deformation
· Assembly
Sheet metal fabrication: Cutting
ii. Water jet cutting
iii. Plasma cutting
Sheet metal fabrication: Forming or Deformation
Bending: Sheet metal bending is one of the most popular deformation processes. A machine known as a Press brake is used to bend sheet metals into V, U, or other complex shapes. With an increase in gauge thicknesses of sheet metals the force required to bend increases.
Stamping: In the stamping process, a hydraulic or mechanical stamping press equipped with a tool and die is used to perform specific tasks like curling, drawing, embossing, flanging, etc
Hemming: Hemming is a process by which the edges of sheet metal are folded over itself or another piece of sheet metal to create a rounded edge. In the sheet metal fabrication process, two types of hemming processes are widely involved. They are roll hemming and conventional die hemming. Conventional hemming is used for mass production. A hemming roller is used for roll hemming.
Spinning: Spinning is a metal fabrication process where a lathe machine is used to rotate the sheet metal against a tool to produce conical or cylindrical shapes.
Sheet metal fabrication: Assembly
Assembly is basically joining sheet metal components produced using above mentioned cutting or bending processes. The common sheet metal assembly process consists of joining by Welding and joining using fasteners.
Welding: In the welding process, sheet metal components are joined together by melting sections with the application of heat to form a solid connection. There are various processes available that are used to weld sheet metals.
Joining using Fasteners: Similar or dissimilar sheet metal parts can easily be joined using fasteners like bolts, screws, rivets, etc.
Brazing: Brazing is a process similar to welding that operates by melting a filler without melting the sheet metals.
Adhesives: Adhesives can be used to hold metal sheets together in conjunction with other joining methods
Advantages and Disadvantages of Sheet Metal Fabrication
As sheet metal fabrication covers a wide area of techniques and methods, the advantages and limitations will vary depending on the process used during fabrication.
Benefits:
i. Sheet metal fabrication is fast and can produce high-quality components.
i. A large number of processes are available with wide range of materials
ii. High strength to weight ratio for sheet metal fabricated parts.
Disadvantage:
i. Each fabrication process has their own limitations.
ii. High initial cost for set up of equipment and tools.
iii. Requirement of skilled labors for each process.
Sheet Metal Fabrication,Custom Sheet Metal Fabrication,Precision Sheet Metal Fabrication,Stainless Steel Sheet Metal Fabrication
Suzhou FCE precision electronics Co., LTD , https://www.sjfukeyifcesz.com